INTRODUCTION
The purpose of this paper is to provide brief, generic descriptions of regulations that are commonly encountered when dealing with flexible tubing. For complete information regarding any of the following specifications, the specification of interest must be viewed in its official form.
Electrical Insulation Regulations
UL/CSA 224
The Underwriters Laboratory standard UL224 and the Canadian Standards Association standard CSA C22.2 No. 198.1 are jointly issued as a common specification to define their requirements for electrical insulation tubing. This common specification, sometimes referred to as UL/CSA 224, applies to entirely extruded compounds made from thermosetting, elastomeric, or thermoplastic polymers. The requirements also cover heat-shrinkable and cross-linked tubing.
Depending on which material is being evaluated (as well as whether or not it’s heat-shrinkable), a specified number of samples of defined sizes must be submitted for testing by the manufacturer. These samples are subjected to a designated number of tests, including those related to:
Depending on which material is being evaluated (as well as whether or not it’s heat-shrinkable), a specified number of samples of defined sizes must be submitted for testing by the manufacturer. These samples are subjected to a designated number of tests, including those related to:
- Physical Properties
- Oil Resistance (Optional)
- Flexibility (Non-Heat-Shrinkable Only)
- Dielectric Voltage Withstand and Breakdown
- Deformation
- Heat Shock
- Cold Bend
- Flammability
- VW-1 (Optional)
- Volume Resistivity
- Secant Modulus
- Eccentricity (Heat-Shrinkable Only)
- Longitudinal Change
- Copper Corrosion
- Copper Stability
- Restricted Recovery (Heat-Shrinkable Only)
- Heat-Resistant Properties (Non-Heat-Shrinkable Only)
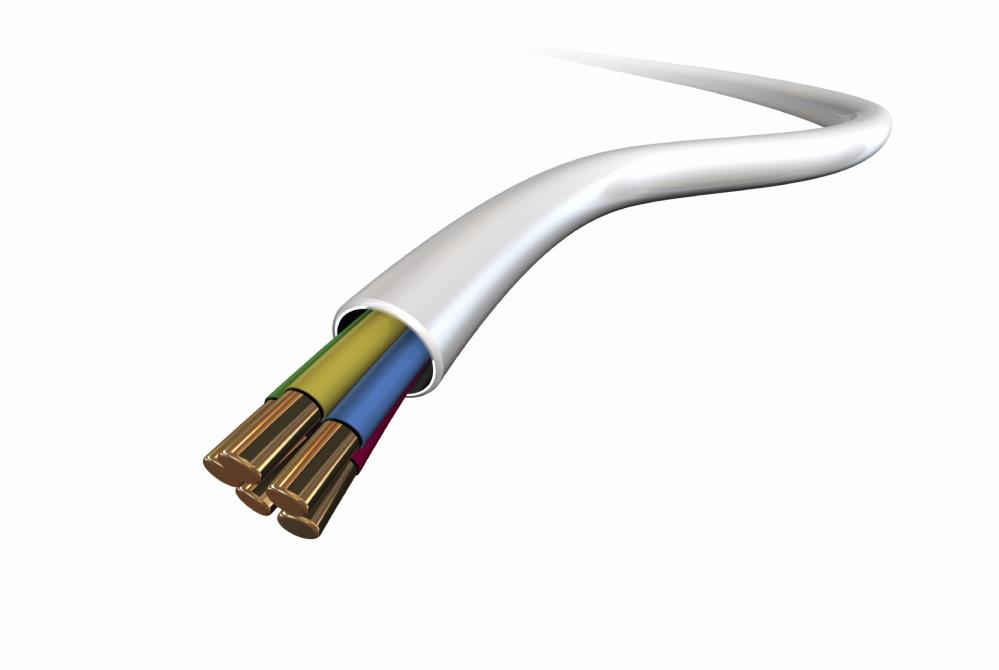
VW-1 is an optional flammability test that is commonly required as a part of UL/CSA 224 certification. All sizing, dielectric strength values, and maximum temperature ratings for the tubing product are defined by UL/CSA and listed in the specification. There are tables which define the passing criteria for each material/dielectric/temperature combination. Once the samples from the manufacturer pass these designated tests at a UL/CSA laboratory, the manufacturer can list their product as being in compliance with UL/CSA 224.
UL and CSA are well-known standards organizations that continually monitor product listings. Therefore having a product UL-listed gives the end user confidence in the product. UL/CSA 224 is commonly required for any tubing being used with consumer goods, including UL-listed tools and appliances.
UL and CSA are well-known standards organizations that continually monitor product listings. Therefore having a product UL-listed gives the end user confidence in the product. UL/CSA 224 is commonly required for any tubing being used with consumer goods, including UL-listed tools and appliances.
AMS-DTL-23053
AMS-DTL-23053 is an SAE specification that establishes guidelines for electrical heat shrinkable tubing. Originally U.S. Military Specification MIL-DTL-23053E, it was adopted by SAE and brought into conformance with SAE standards. The specification is separated into a main document which defines testing and inspection guidelines, and numerous sub-documents which define sizing and passing criteria for each material type. For example, AMS-DTL-23053/5 defines sizing and test criteria for flexible, cross-linked polyolefin heat shrinkable tubing.
In addition to sizing and visual inspection requirements, there are a number of physical tests required by AMS-DTL-23053. These tests cover the following:
In addition to sizing and visual inspection requirements, there are a number of physical tests required by AMS-DTL-23053. These tests cover the following:
- Specific Gravity
- Dielectric Constant
- Fungus Resistance
- Corrosion
- Tensile Strength
- Ultimate Elongation
- Dielectric Strength
- Volume Resistivity
- Low Temperature Flexibility
- Heat Resistance
- Water Absorption
- Flammability
- Fluid Resistance
- Sealing Efficiency
- Heat Shock
- Restricted Shrinkage
- Shelf Life
- Cold Impact
- Modulus

AMS-DTL-23053 is widely recognized for all types of heat-shrinkable tubing. It is perhaps most commonly referenced when specifying cross-linked polyolefin heat shrink tubing for automotive(under the hood) applications.
EU REACH Regulation
The European Union’s REACH Regulation (Registration, Evaluation, Authorization, and Restriction of Chemicals) aims to improve the protection of human health and the environment through better identification of the properties of chemical substances. It places greater responsibility on the industry to manage the risks from chemicals and provides safety information on the substances.
Most if not all tubing products are considered “Articles” under the regulation and do not contain any substances intended for release. Therefore the substances should not be required to be registered with the EU. A common substance contained in flexible PVC tubing is DEHP. Because the European Chemicals Agency (ECHA) lists DEHP as a Substance of Very High Concern (SVHC), the manufacturer is required to report tubing containing more than 0.1% DEHP by weight.
Most if not all tubing products are considered “Articles” under the regulation and do not contain any substances intended for release. Therefore the substances should not be required to be registered with the EU. A common substance contained in flexible PVC tubing is DEHP. Because the European Chemicals Agency (ECHA) lists DEHP as a Substance of Very High Concern (SVHC), the manufacturer is required to report tubing containing more than 0.1% DEHP by weight.
EU Directive 2002/95/EC (RoHS), 2011/65/EU (RoHS 2) and 2015/863 (RoHS 3)
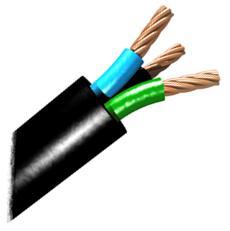
The European Union Directive 2002/95/EC (sometimes referred to as the Restriction of Hazardous Substances Directive, or RoHS) restricts the use of certain substances in various electrical equipment, including electrical tubing or sleeving. This directive requires that electrical tubing and sleeving not contain lead, mercury, cadmium, hexavalent chromium, polybrominated biphenyls (PBB) or polybrominated diphenyl ethers (PBDE). The RoHS directive took effect in July of 2006.
European Union Directive 2011/65/EU (commonly called RoHS 2) became effective on January 3, 2013. It did not add any new substance but did expand the scope and regulatory structure.
Delegated Directive EU 2015/863 (commonly called RoHS 3) was published on June 4, 2015 and will go into effect on July 22, 2019. This revision added four phthalate substances which will be prohibited. These four are Bis (2-ethylhexyl) phthalate (DEHP), Butyl benzyl phthalate (BBP), Dibutyl phthalate (DBP) and Diisobutyl phthalate (DIBP).
European Union Directive 2011/65/EU (commonly called RoHS 2) became effective on January 3, 2013. It did not add any new substance but did expand the scope and regulatory structure.
Delegated Directive EU 2015/863 (commonly called RoHS 3) was published on June 4, 2015 and will go into effect on July 22, 2019. This revision added four phthalate substances which will be prohibited. These four are Bis (2-ethylhexyl) phthalate (DEHP), Butyl benzyl phthalate (BBP), Dibutyl phthalate (DBP) and Diisobutyl phthalate (DIBP).
FMVSS 302
Federal Motor Vehicle Safety Standard (FMVSS) Number 302 is entitled “Flammability of Interior Materials.” This standard specifies burn resistance requirements for materials used in the occupant compartments of motor vehicles. The purpose of the standard is to reduce the deaths and injuries to passengers caused by vehicle fires, especially those originating in the interior of the vehicle. The standard applies to passenger cars, multipurpose passenger vehicles, trucks, and busses.
Electrical tubing is often required to meet FMVSS 302 if the tubing is to be used in the interior of a vehicle. The test measures the burn rate of a slab of the material in question. In order to pass the test, the material must not burn, nor transmit a flame front across its surface, at a rate faster than 4 inches per minute.
Electrical tubing is often required to meet FMVSS 302 if the tubing is to be used in the interior of a vehicle. The test measures the burn rate of a slab of the material in question. In order to pass the test, the material must not burn, nor transmit a flame front across its surface, at a rate faster than 4 inches per minute.
MIL-I-631
MIL-I-631 is a military specification for flexible electrical insulating materials. It covers insulation types such as film, tape, and tubing, as well as materials such as polyethylene, PET, and PVC, among others. It offers two classes, one for fungus-resistant material and one without this requirement. There are also different temperature grades, and a flame-resistance category for tubing. Depending on the Type/Form/Grade/Class/Category of the product being tested, there are various tests that must be performed. These tests include flexibility after aging, cold bend, flame resistance, oil resistance-flexibility, corrosion, fungus-resistance, chemical analysis, and storage stability tests.
IL-I-631 is commonly referenced when the combination of flame resistance and low temperature performance is required. Snowmobile, ATV, and motorcycle manufacturers commonly reference this specification when defining their electrical tubing requirements.
IL-I-631 is commonly referenced when the combination of flame resistance and low temperature performance is required. Snowmobile, ATV, and motorcycle manufacturers commonly reference this specification when defining their electrical tubing requirements.
MIL-I-7444
MIL-I-7444 is also a military specification for flexible electrical insulation, but it is focused strictly on PVC tubing. It differentiates between clear and pigmented tubing, and also specifies two different brittle temperature and flame resistance classes. Required testing for this specification includes tests for physical properties, flame resistance, brittle point, corrosion, oil aging, fungus resistance, and wet and dry dielectric strength. Marking, workmanship, and inspection guidelines are also specified for the tubing and its packaging.
Like MIL-I-631, MIL-I-7444 is commonly referenced when both high flame resistance and low temperature performance are needed. The specification requires a good combination of UV resistance, anti-fungal properties, flame resistance, and extreme low-temperature flexibility. Therefore it is commonly referenced for deep-freeze freezer and military aircraft applications.
Like MIL-I-631, MIL-I-7444 is commonly referenced when both high flame resistance and low temperature performance are needed. The specification requires a good combination of UV resistance, anti-fungal properties, flame resistance, and extreme low-temperature flexibility. Therefore it is commonly referenced for deep-freeze freezer and military aircraft applications.
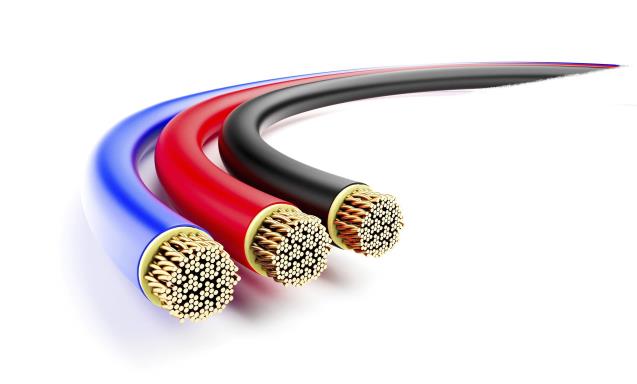
MEDICAL REGULATIONS
USP Class VI
The United States Pharmacopeia Convention (USP) is a scientific nonprofit organization that sets standards for the quality, purity, identity, and strength of medicines, food ingredients, and dietary supplements manufactured and used worldwide. USP biocompatibility testing evaluates the suitability of a medical device to be used in various degrees of body contact (surface device, implant device, etc.). Many medical devices require USP Class VI certification; therefore, tubing used in the device may need to be certified as well.
USP biocompatibility testing is broken up into six classes, the most stringent (and most common for medical tubing) being Class VI. Class VI specifies that the Intracutaneous Injection, Systemic Toxicity, and Implant tests be performed. Simply put, these three tests consist of injecting mice or rabbits with the product being tested, and evaluating the animals for any systemic reactions to the injections. If a given material is certified to USP Class VI, this does not mean that a product made only of this material is automatically certified. The final product (tubing, in this case) must be tested in order to achieve certification.
USP biocompatibility testing is broken up into six classes, the most stringent (and most common for medical tubing) being Class VI. Class VI specifies that the Intracutaneous Injection, Systemic Toxicity, and Implant tests be performed. Simply put, these three tests consist of injecting mice or rabbits with the product being tested, and evaluating the animals for any systemic reactions to the injections. If a given material is certified to USP Class VI, this does not mean that a product made only of this material is automatically certified. The final product (tubing, in this case) must be tested in order to achieve certification.
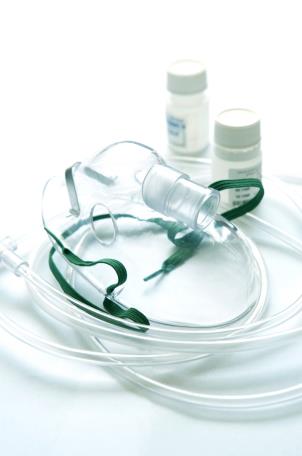
ISO 10993
Another biocompatibility standard is ISO 10993. The 10993 standard was developed for medical device and dental materials by the International Organization for Standardization (ISO). It defines three categories for types of body contact (surface, external communicating, implant) and three categories for exposure periods (limited, prolonged, permanent contact). The standard is broken up into 20 parts. Part 1 of the standard directs the selection of tests that may be necessary for a given type of device. The remaining 19 parts of the standard consist of the specific tests for each category. Depending on the nature and duration of human contact of the device, some or all of the following tests may be recommended: cytotoxicity, hemocompatibility, carcinogenicity, genotoxicity, subacute/subchronic toxicity, irritation or intracutaneous reactivity, sensitization, implantation, chronic toxicity, and acute systemic toxicity. Since each medical device is used differently, it must be decided which of the above tests are required to be completed for a given device.
FDA Title 21, The Code of Federal Regulations
The Food and Drug Administration (FDA) is the federal agency responsible for ensuring that food, drugs, and medical devices are safe and effective for humans. The FDA also ensures that these products are honestly, accurately, and informatively represented to the public. The agency is also responsible for biologics, cosmetics, radiation-emitting electronic products, and veterinary products. The Code of Federal Regulations (CFR) is the published rules and regulations of the Federal Government of the United States. Title 21 of the CFR covers food and drugs within the United States for the FDA.FDA Title 21 regulates plastics used in food contact applications. These regulations and requirements are found in Title 21, Section 177 of the CFR. Sometimes, medical device manufacturers require FDA Title 21 approval for materials used in their device. This ensures that only non-toxic materials are being utilized intheir products.
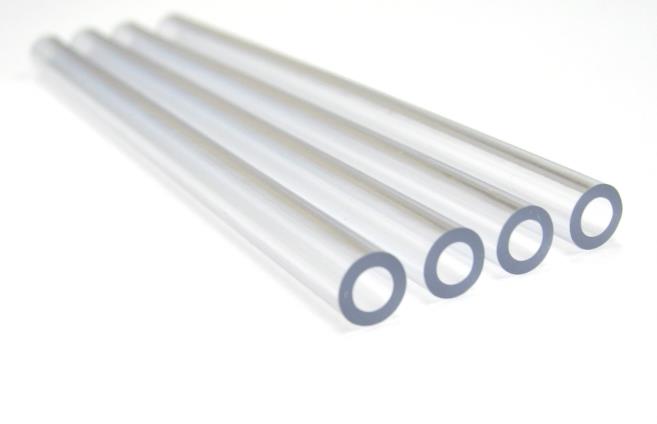
EU Regulation 1907/2006 (DEHP Content)
This European Community Regulation, otherwise known as REACH, deals with the Registration, Evaluation, Authorization, and Restriction of Chemical substances. The aim of this regulation is to identify properties of chemical substances in order to help protect human health and the environment. The European Chemicals Agency (ECHA) manages the evaluation of various chemicals and determines whether or not each needs to be listed as a Substance of Very High Concern (SVHC).
One chemical commonly used in flexible PVC tubing is the general-purpose plasticizer DEHP (di-2-ethylhexyl phthalate). The ECHA lists DEHP as a substance of very high concern. The European Union requires that the concentration of DEHP must not exceed 0.1% (1000 ppm) by mass in plasticized materials used in toys and childcare articles. While some PVC compounds are formulated without DEHP, nearly all of them are subjected to cross-contamination in compounding factories and therefore can contain trace levels of DEHP. The EU requires that these trace levels be below 1000 ppm.
One chemical commonly used in flexible PVC tubing is the general-purpose plasticizer DEHP (di-2-ethylhexyl phthalate). The ECHA lists DEHP as a substance of very high concern. The European Union requires that the concentration of DEHP must not exceed 0.1% (1000 ppm) by mass in plasticized materials used in toys and childcare articles. While some PVC compounds are formulated without DEHP, nearly all of them are subjected to cross-contamination in compounding factories and therefore can contain trace levels of DEHP. The EU requires that these trace levels be below 1000 ppm.
Consumer Product Safety Improvement Act (Phthalate Content)
The United States Consumer Product Safety Commission (CPSC) analyzes consumer products in order to help protect the public from unreasonable risks of injury or death. It is responsible for regulating any products that pose a fire, electrical, chemical, or mechanical hazard to children. In 2008 it passed the Consumer Product Safety Improvement Act (CPSIA). The purpose of this Act is to establish consumer product safety standards and other safety requirements for children’s products.
Section 108 of the CPSIA prohibits the sale of any childcare article containing a concentration of phthalates higher than 0.1%. Therefore, with regard to flexible tubing, it is very similar to the EU requirement. The difference is that the EU restricts only DEHP, but the CPSIA restricts all phthalate plasticizers.
Section 108 of the CPSIA prohibits the sale of any childcare article containing a concentration of phthalates higher than 0.1%. Therefore, with regard to flexible tubing, it is very similar to the EU requirement. The difference is that the EU restricts only DEHP, but the CPSIA restricts all phthalate plasticizers.
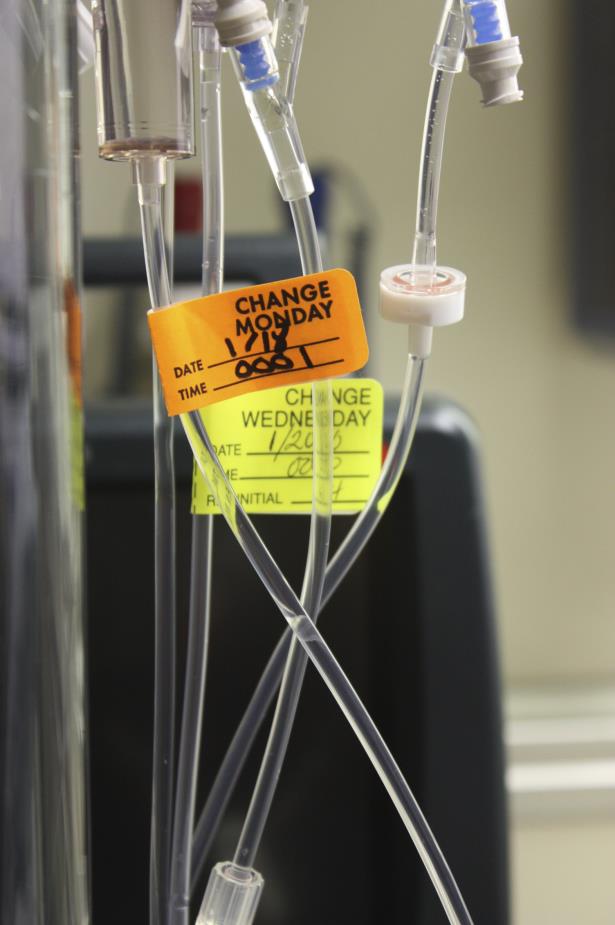
FOOD & BEVERAGE REGULATIONS
NSF-51
NSF International is an independent, non-government organization of scientists, technicians, educators and engineers. It serves the government, industry, and consumers by achieving solutions to problems relating to public health and the environment. NSF Standards are developed through involvement of those who are directly affected by the scope of the standard. This process ensures balanced input from industry representatives, public health officials, and consumer representatives.
NSF Standard 51 is applicable to complete pieces of food equipment, as well as components of food equipment such as tubing, sealants, gaskets, and valves. Component materials in the food zone of the food equipment must not affect the characteristics of the food by imparting color, taste or odor to the food. Component materials are regulated as indirect food additives of the US Code of Federal Regulations (FDA Title 21). In addition to material requirements, NSF Standard 51 covers surface cleanability, corrosion resistance, and special requirements for specific types of materials. The certification process begins with a physical evaluation of the product and an extensive review of the materials used in the product. NSF then decides if the product is suitable for use with any or all of the following types of food/beverages: aqueous food, bakery products, dairy products, dry solids, oils and fats, and alcoholic beverages. NSF also designates a maximum temperature at which the product can be used. NSF-certified manufacturers are audited on an annual basis.
If tubing is needed in food equipment and it is required to contact any food or beverage, it is likely a requirement that the tubing product be listed with NSF 51.
NSF Standard 51 is applicable to complete pieces of food equipment, as well as components of food equipment such as tubing, sealants, gaskets, and valves. Component materials in the food zone of the food equipment must not affect the characteristics of the food by imparting color, taste or odor to the food. Component materials are regulated as indirect food additives of the US Code of Federal Regulations (FDA Title 21). In addition to material requirements, NSF Standard 51 covers surface cleanability, corrosion resistance, and special requirements for specific types of materials. The certification process begins with a physical evaluation of the product and an extensive review of the materials used in the product. NSF then decides if the product is suitable for use with any or all of the following types of food/beverages: aqueous food, bakery products, dairy products, dry solids, oils and fats, and alcoholic beverages. NSF also designates a maximum temperature at which the product can be used. NSF-certified manufacturers are audited on an annual basis.
If tubing is needed in food equipment and it is required to contact any food or beverage, it is likely a requirement that the tubing product be listed with NSF 51.
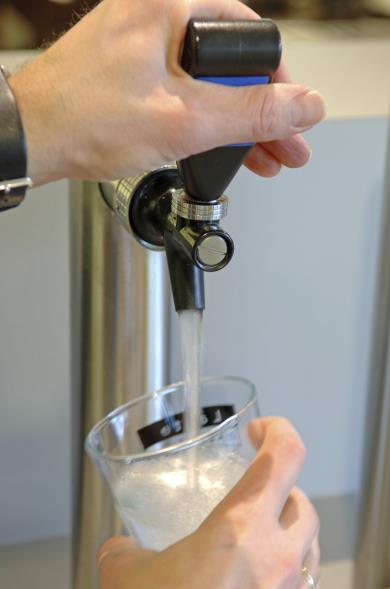
NSF-61
NSF Standard 61, entitled Drinking Water System Components, is the nationally recognized health effects standard for all devices, components, and materials which contact drinking water. NSF 61 establishes minimum requirements for the control of potential adverse human health effects from products that contact drinking water. It includes criteria for testing and evaluating products to ensure they do not leach contaminants into the water that would result in health concerns.
Products included under NSF Standard 61 are pipe, tubing/hose, fittings, protective and barrier materials, joining and sealing materials, process media, mechanical devices, and potable water materials. The first step of NSF 61 certification is disclosure by the manufacturer of all water contact materials in the product and disclosure by the manufacturer’s material suppliers of all chemical ingredients in the materials. NSF then reviews the formulation, and follows with a plant audit, sample collection, laboratory testing, and a toxicology evaluation. If the product is deemed acceptable, certification is granted and the product is inspected and reviewed by NSF on an annual basis.
Products included under NSF Standard 61 are pipe, tubing/hose, fittings, protective and barrier materials, joining and sealing materials, process media, mechanical devices, and potable water materials. The first step of NSF 61 certification is disclosure by the manufacturer of all water contact materials in the product and disclosure by the manufacturer’s material suppliers of all chemical ingredients in the materials. NSF then reviews the formulation, and follows with a plant audit, sample collection, laboratory testing, and a toxicology evaluation. If the product is deemed acceptable, certification is granted and the product is inspected and reviewed by NSF on an annual basis.
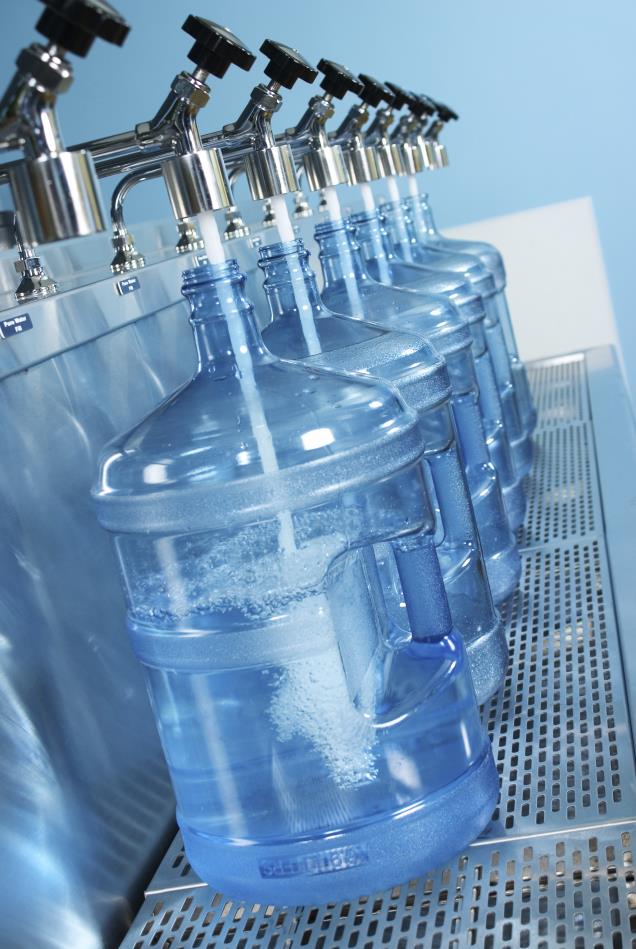
NSF-FDA Title 21, The Code of Federal Regulations61
FDA Title 21 regulates plastics used in food contact applications. These regulations and requirements are found in Title 21, Section 177 of the CFR. The FDA provides a list of ingredients that are acceptable for use in food contact applications. For more detailed information see the FDA Title 21 entry in the Medical Regulations section.
3-A
3-A is similar to NSF Standard 51 in that it regulates food equipment; however, it focuses entirely on the dairy industry. 3-A formulates sanitary standards and accepted practices for the sanitary design, fabrication, installation and cleanability of dairy equipment. 3-A Sanitary Standards provide material specifications, design criteria and other necessary information for equipment types to satisfy public health concerns. The goal of 3-A is to protect consumable dairy products from contamination and to ensure that all product surfaces can be cleaned. 3-A-certified tubing must pass testing at a qualified independent laboratory prior to receiving 3-A approval.
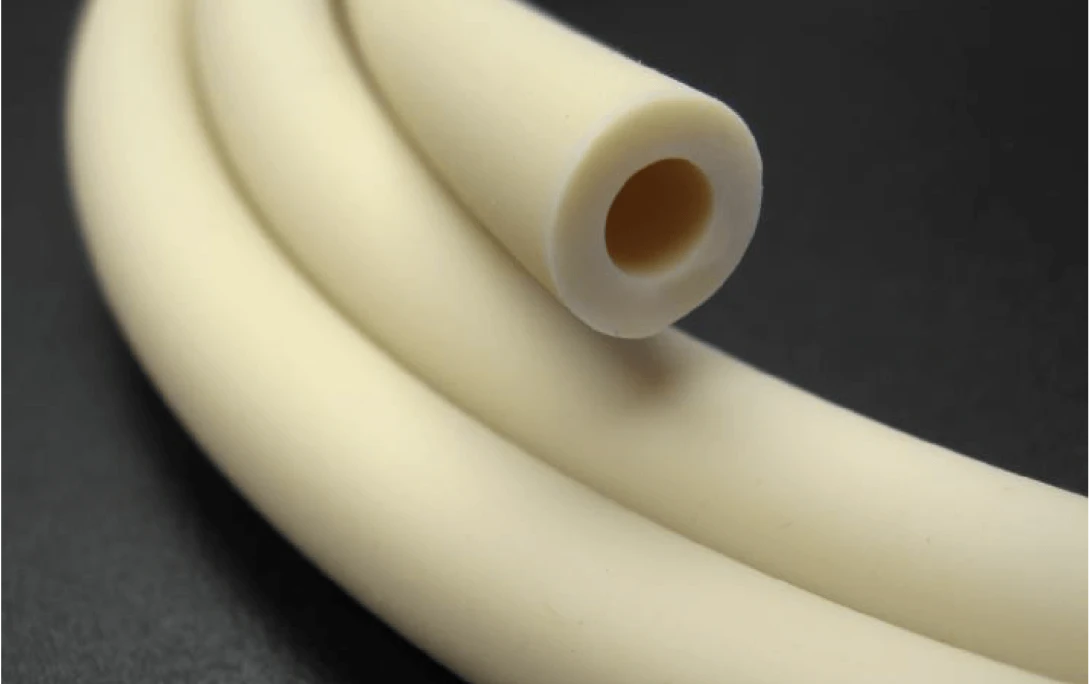