Abstract
Peristaltic pumps are used in a wide variety of applications because they provide a means for transporting sensitive fluids without exposure to mechanical pistons or moving parts. Material selection is critical because the tubing comes in contact with the fluid. This whitepaper provides a general overview of how a peristaltic pump works and compares six different peristaltic pump tubing material options with regards to hardness, size, chemical compatibility, and durability.
Tubing Materials:
- High Molecular Weight, Flexible Polyvinyl Chloride (PVC)
- Standard Flexible Polyvinyl Chloride (PVC)
- Peroxide Cured Silicone
- Thermoplastic Vulcanizate (TPV)
- Thermoplastic Elastomer (TPE)
- Viton Rubber
How a Peristaltic Pump Works
In its principle form, a peristaltic pump operates in a similar manner to the human esophagus. The word peristalsis is actually defined as “successive waves of involuntary contraction passing along the walls of a hollow muscular structure and forcing the contents onward” (Merriam-Webster). So before reading the next few paragraphs, take a drink of water and think about how this fluid is being conveyed.
The mechanical peristaltic pump is made up of a few simple components that combine to form a positive displacement pump. An electric motor provides power to a roller which rotates and squeezes flexible tubing along the pump casing. This compression and subsequent relaxation of the tube, concurrently draws fluid in and pushes it out of the other end. The following steps and pictures provide a detailed explanation of the peristaltic pumping process.
The mechanical peristaltic pump is made up of a few simple components that combine to form a positive displacement pump. An electric motor provides power to a roller which rotates and squeezes flexible tubing along the pump casing. This compression and subsequent relaxation of the tube, concurrently draws fluid in and pushes it out of the other end. The following steps and pictures provide a detailed explanation of the peristaltic pumping process.
Step 1:
- The peristaltic pump rotates and creates a seal at the suction side of the pump. It also encapsulates the blue section of fluid and starts to push it through the pump.
- The red section of fluid is being forced out the discharge end of the pump.
- As the tubing begins to recover, the green section of fluid is sucked into the pump.
Step 2:
- As the pump rotates, it continues to push the blue region of fluid.
- The red section of the fluid is now completely discharged.
- The green section of fluid continues to be pulled into the pump.
Step 3:
- As the pump rotates, it continues to push the blue region of fluid.
- The green section of fluid continues to be pulled into the pump.
Step 4:
- As the pump rotates, it continues to push the blue region of fluid.
- The green section of fluid is now encapsulated by the rollers.
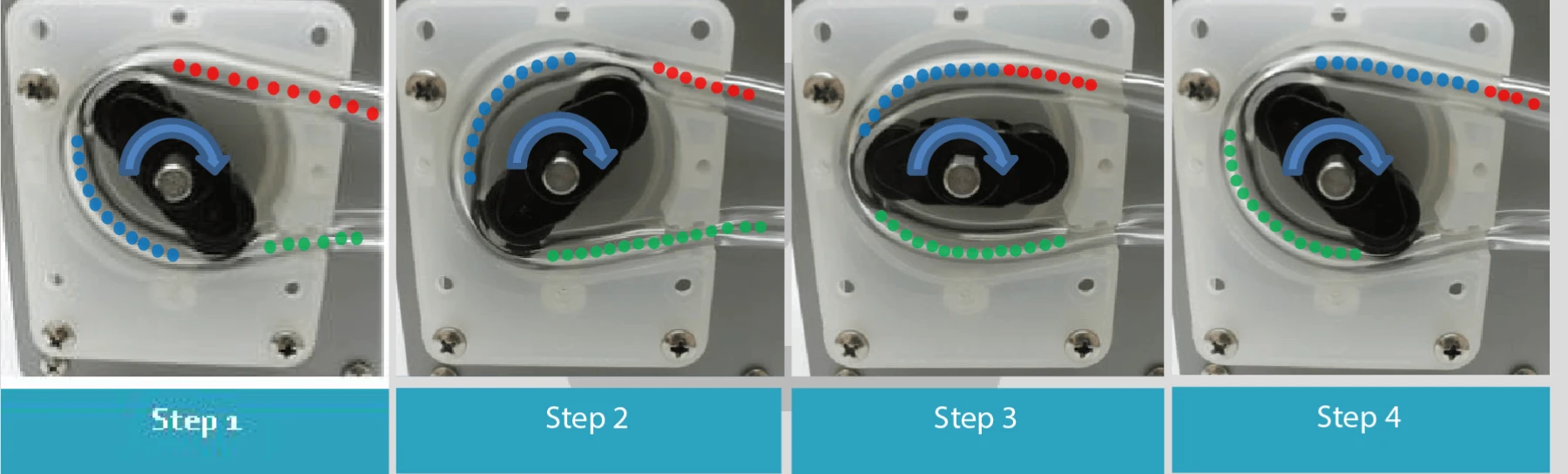
Tubing Hardness
The peristaltic pump transports fluid by squeezing tubing between a roller and the pump housing. The tubing must be flexible enough to allow the motor to rotate and push the fluid through the tubing. If the tubing is too hard, it will put additional load on the motor which may reduce the life of the pump or stop it from working altogether. A general guideline for peristaltic pumps is to select a hardness value that is between 50 –65 on the shore A hardness scale.
Some applications require that a filter be placed at the discharge end of the pump. As the filter removes impurities from the flow stream, it can become partially blocked. This will create backpressure in the pump, which could cause the tubing to burst if it exceeds the pressure rating of the tube. In these cases, a harder material may be required to prevent the backpressure from exceeding the burst pressure rating of the tubing. Both the tubing manufacturer and peristaltic pump manufacturer should be able to help determine the material hardness required for the application.
Some applications require that a filter be placed at the discharge end of the pump. As the filter removes impurities from the flow stream, it can become partially blocked. This will create backpressure in the pump, which could cause the tubing to burst if it exceeds the pressure rating of the tube. In these cases, a harder material may be required to prevent the backpressure from exceeding the burst pressure rating of the tubing. Both the tubing manufacturer and peristaltic pump manufacturer should be able to help determine the material hardness required for the application.
Tubing Size
Peristaltic pump manufacturers often recommend a specific brand of tubing to be used in conjunction with their pumps to ensure that the user is using the correct material, hardness, and size. Much like the tubing hardness, irreversible damage can be caused to the pump if it is sized incorrectly. It is never safe to assume that a standard size tube will work with a pump, even if it has the same inside diameter. The wall thickness of the tubing must match up with the gap between the roller and the housing in the peristaltic pump. Even a difference of .005” in wall thickness can significantly reduce the life of the pump, or stop it from working altogether. As shown in Figure 1, a thin wall thickness can prevent a seal from being created and the pump will not work efficiently. Figure 2 illustrates a wall thickness that is too thick, resulting in increased tubing wear and reduced pump life.
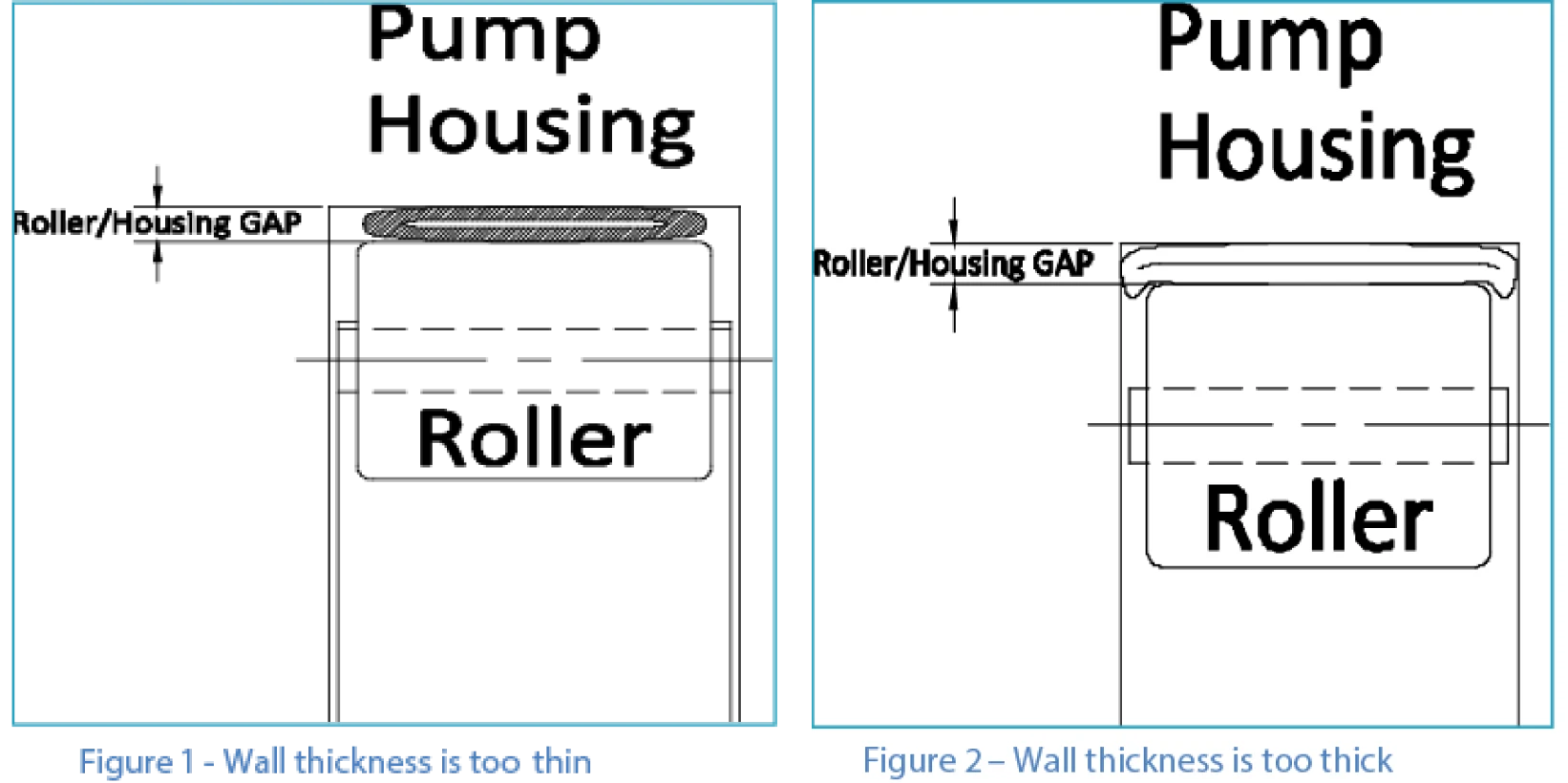
Chemical Compatibility
Since the transported fluid of a peristaltic pump only comes into contact with one surface (tubing), it can be fairly straight-forward to select a material. There isn’t a catch-all material for peristaltic pumps that will work with every chemical, so it is important to understand the effects of each. The ratings listed below represent an overall generalization of a material family. All tubing should be tested under actual conditions to ensure suitability for a specific application.
Ratings:
Excellent = Tubing should not experience degradation due to chemicals and is most likely suitable for long term exposure.
Good = Tubing will experience some degradation due to chemicals exposure.
Fair = Tubing may experience significant degradation
Poor = Material is not recommended for applications
Good = Tubing will experience some degradation due to chemicals exposure.
Fair = Tubing may experience significant degradation
Poor = Material is not recommended for applications
Chemicals
Chlorine: = A chemical that is commonly used for water purification.
Water (Distilled): = Water that has had its impurities removed through distillation.
Oil (ASTM #1): = An oil that is often used to indicate compatibility with lubricating oils & greases.
Isopropyl Alcohol: = An industrial solvent that evaporates quickly and leaves minimal residue.
Hydrochloric Acid: A highly corrosive, strong mineral acid.
Sodium Hydroxide: A strong base that is commonly used in the chemical industry and paper production. It is also known as lye or caustic soda.
Water (Distilled): = Water that has had its impurities removed through distillation.
Oil (ASTM #1): = An oil that is often used to indicate compatibility with lubricating oils & greases.
Isopropyl Alcohol: = An industrial solvent that evaporates quickly and leaves minimal residue.
Hydrochloric Acid: A highly corrosive, strong mineral acid.
Sodium Hydroxide: A strong base that is commonly used in the chemical industry and paper production. It is also known as lye or caustic soda.
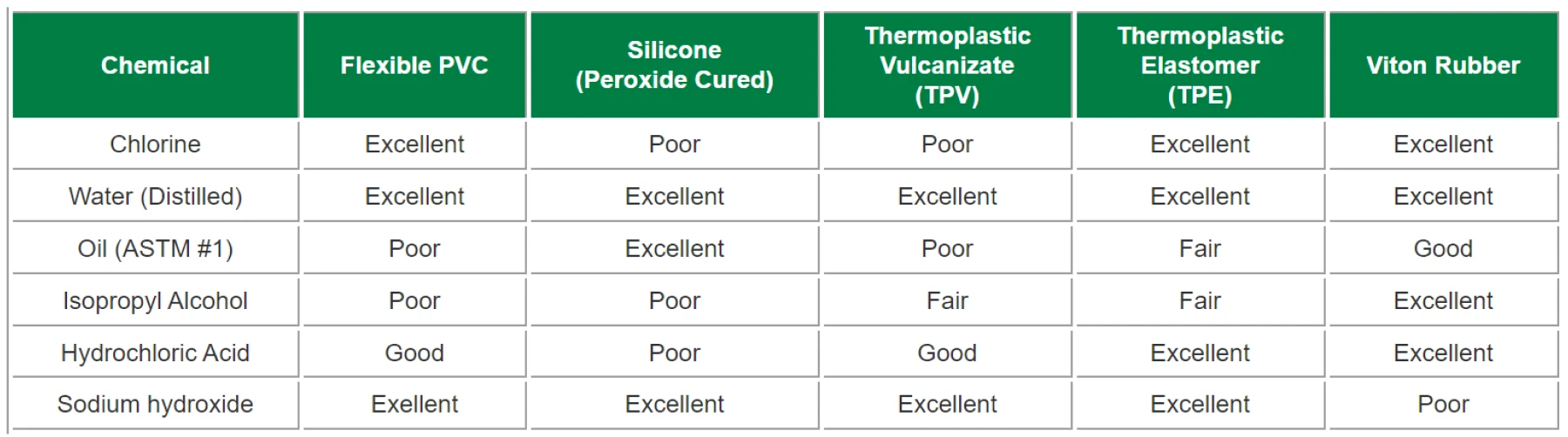
Tubing Flow Rate (Continuous Pumping Comparison)
Testing was performed on six different tubing materials that were placed inside a two roller peristaltic pump that ran at 100 RPM for a total of 24 hours. The tubing size was 1/4” ID x 7/16” OD and tested at room temperature. The data can be found in the chart below which shows how each tube responded to over 280,000 compression and relaxation cycles of the peristaltic pump. Excluding the Viton rubber tubing, the different materials performed fairly similarly, maintaining a flow rate within 3% of the starting flow rate.
This test illustrates that when a pump is running continuously over a short duration, low cost materials such as PVC can be just as effective as a high cost silicone. The pump rollers were constantly in motion, so the tubing was not in a compressed state for long durations. In this situation, the superior compression set properties of a material like silicone are less important. The Viton rubber exhibited very poor dynamic wear properties and did not maintain a consistent flow rate
This test illustrates that when a pump is running continuously over a short duration, low cost materials such as PVC can be just as effective as a high cost silicone. The pump rollers were constantly in motion, so the tubing was not in a compressed state for long durations. In this situation, the superior compression set properties of a material like silicone are less important. The Viton rubber exhibited very poor dynamic wear properties and did not maintain a consistent flow rate
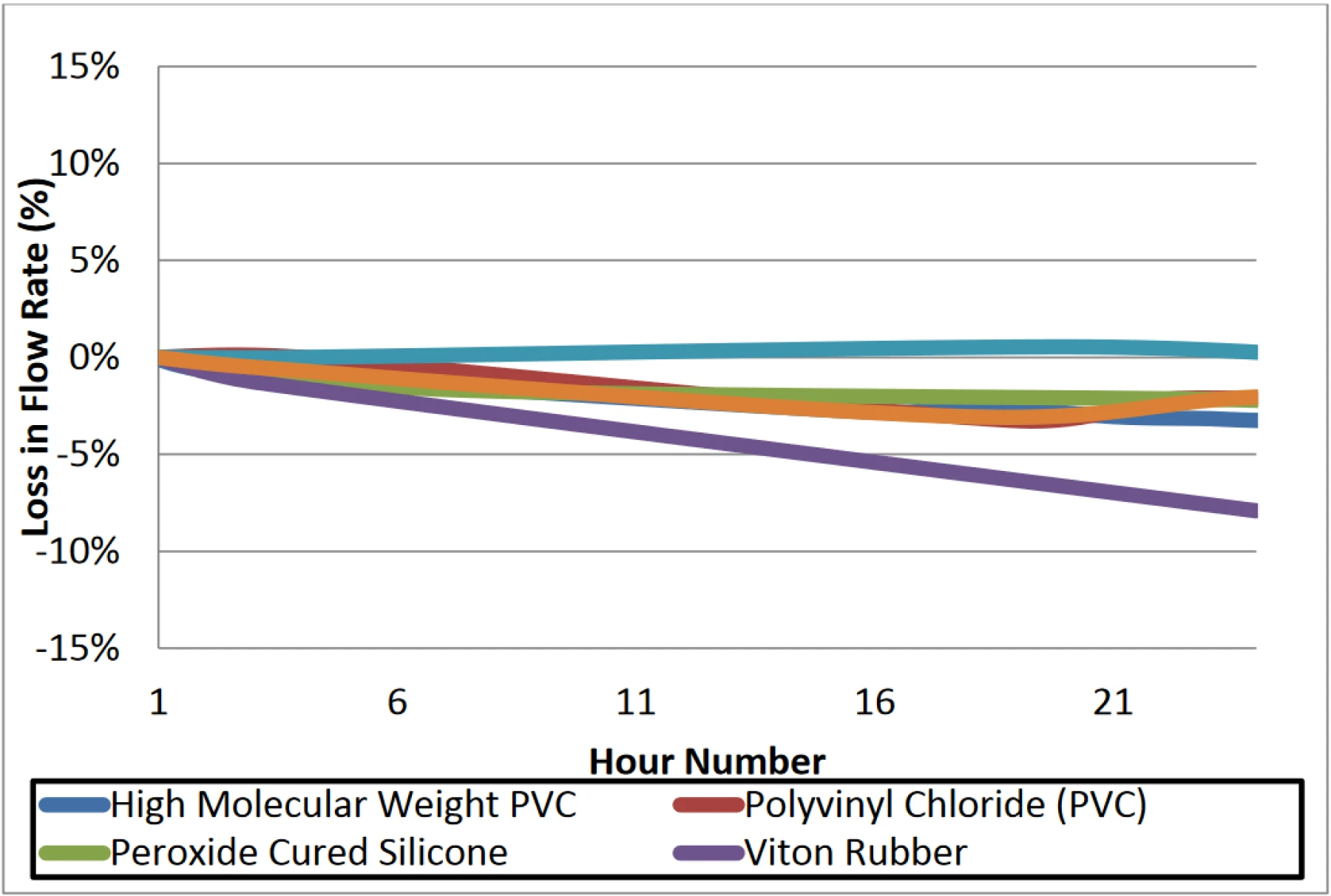
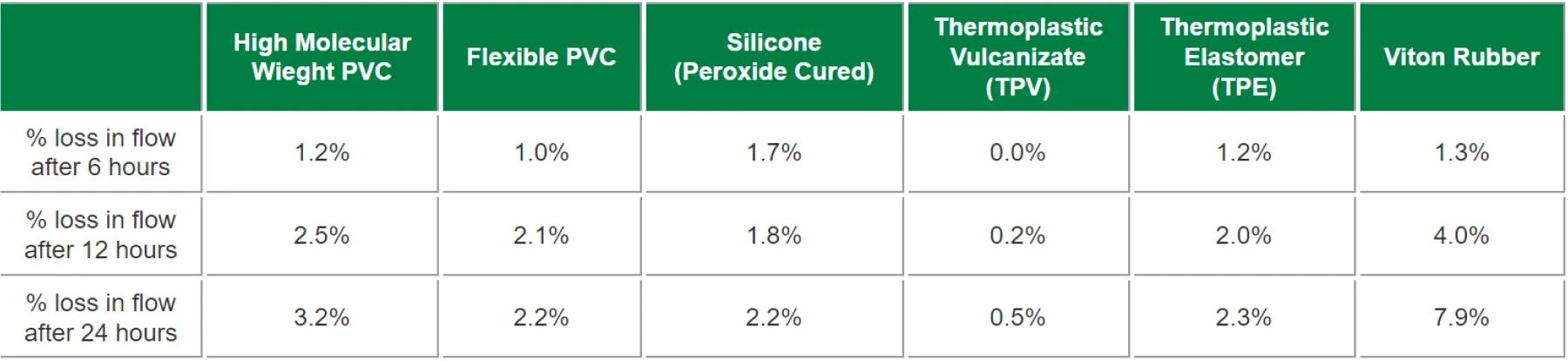
Tubing Deformation (Intermittent Pumping Comparison)
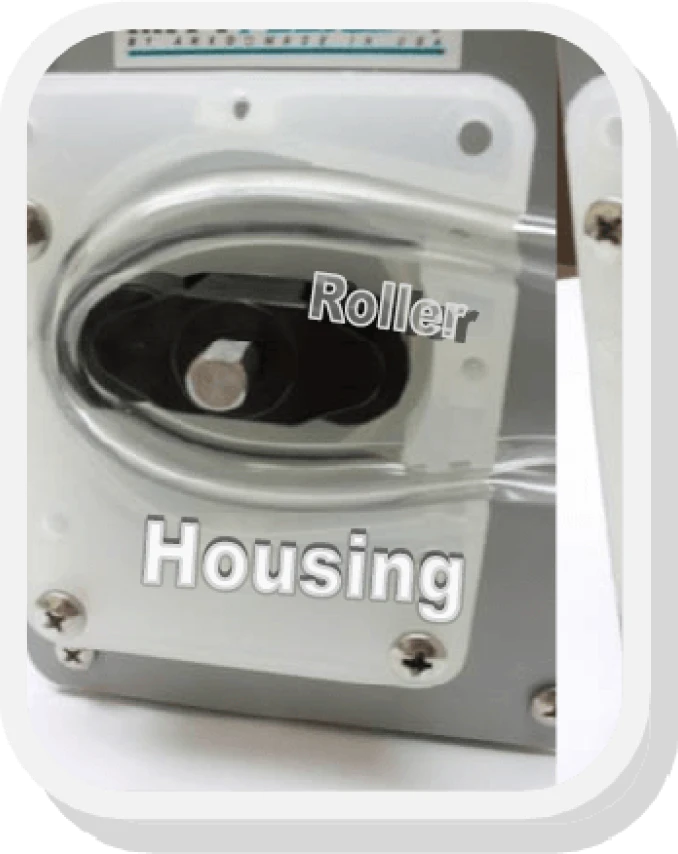
An Intermittent pump test was performed on six different tubing materials that were placed inside a two roller peristaltic pump that ran at 50 RPM for a total of four cycles. The tubing size was 1/4” ID x 7/16” OD and tested at room temperature.
The pump was left idle during this test, causing the tubing to be squeezed between the roller and the housing for long periods of time. The tubing will tend to stay in this compressed state and not fully recover to it’s original diameter after it is released. This reduces the overall suction and subsequent flow of the pump. The flow rate varied significantly during each cycle because the roller compressed a new location at the end of each cycle. The silicone material was the only tubing that maintained a steady flow rate throughout this test.
The pump was left idle during this test, causing the tubing to be squeezed between the roller and the housing for long periods of time. The tubing will tend to stay in this compressed state and not fully recover to it’s original diameter after it is released. This reduces the overall suction and subsequent flow of the pump. The flow rate varied significantly during each cycle because the roller compressed a new location at the end of each cycle. The silicone material was the only tubing that maintained a steady flow rate throughout this test.
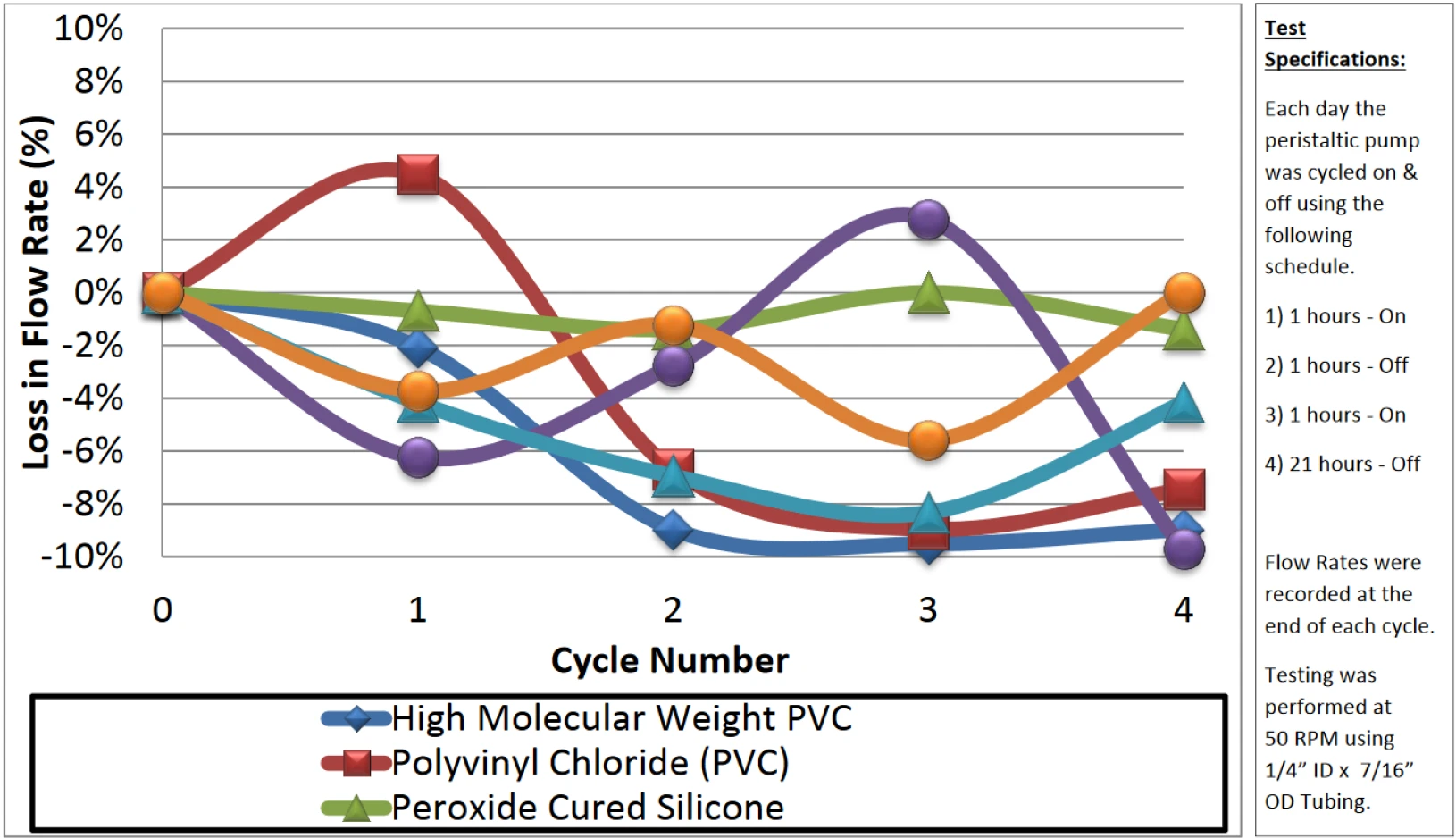
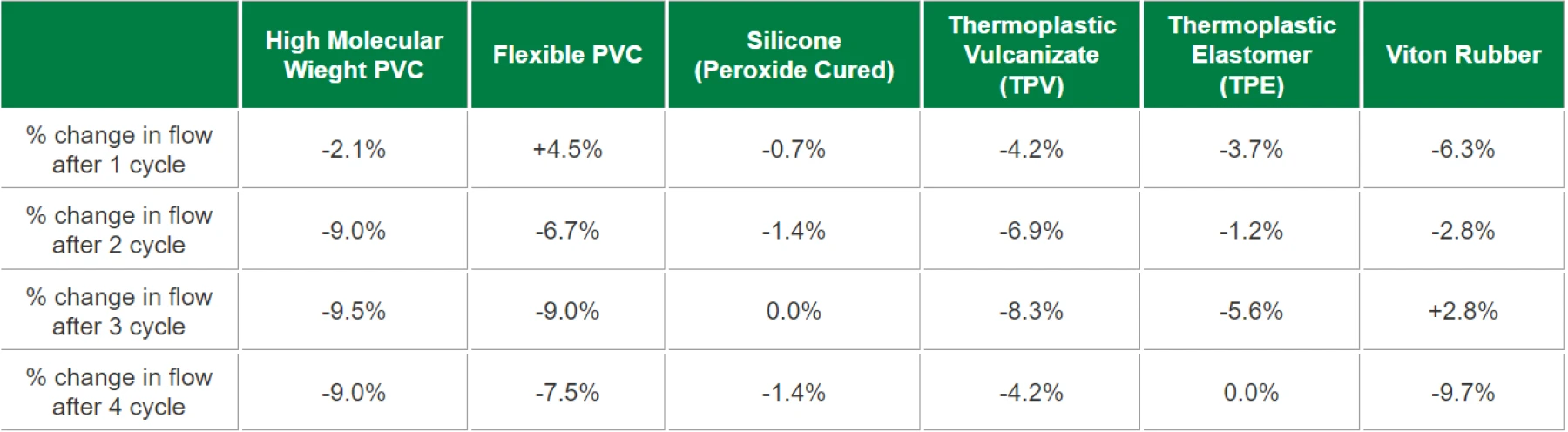
Summary
Tubing hardness, size, and chemical compatibility are all important considerations to take into account when selecting a material for a peristaltic pump application. It is easy to overlook any one of these design considerations, so it is important to work directly with either the tubing or peristaltic pump manufacturer regarding material selection and to perform inhouse testing prior to tubing approval.
This paper offers general guidelines that give a good starting point for most applications. Peristaltic pump tubing is generally between 50 - 65 Shore A hardness and often sold with very tight tolerances on the ID and wall thickness. Since the tubing is the only surface that the fluid is exposed to, the chemical compatibility chart included with this report provides a good way to narrow down the material options.
All of the six materials discussed in this paper were tested in both a continuous and intermittent operating conditions. During the continuous testing, most of the materials performed very similarly over the short timeframe. This suggests that overlooked materials such as PVC might meet the needs of a short-term, one time use medical applications. During the intermittent testing, Silicone stood out as the optimum material choice because of it’s excellent compression set characteristics.
This paper offers general guidelines that give a good starting point for most applications. Peristaltic pump tubing is generally between 50 - 65 Shore A hardness and often sold with very tight tolerances on the ID and wall thickness. Since the tubing is the only surface that the fluid is exposed to, the chemical compatibility chart included with this report provides a good way to narrow down the material options.
All of the six materials discussed in this paper were tested in both a continuous and intermittent operating conditions. During the continuous testing, most of the materials performed very similarly over the short timeframe. This suggests that overlooked materials such as PVC might meet the needs of a short-term, one time use medical applications. During the intermittent testing, Silicone stood out as the optimum material choice because of it’s excellent compression set characteristics.
References
- Chemical Resistance Chart. (n.d.). Retrieved from
www.coleparmer.com/Chemical-Resistance - Chemical Resistance Chart. (n.d.). Retrieved from www.omega.com/pdf/tubing/technical_section/chemical_chart_1.asp
- How do dosing pumps, hose pumps work. (n.d.). Retrieved from https://www.verderflex.com/Pump_Technology/How_do_peristaltic_pumps_work
- Merriam-Webster Dictionary Retrieved from
https://www.merriam-webster.com/dictionary/peristalsis
Peristaltic Pump Tubing Options
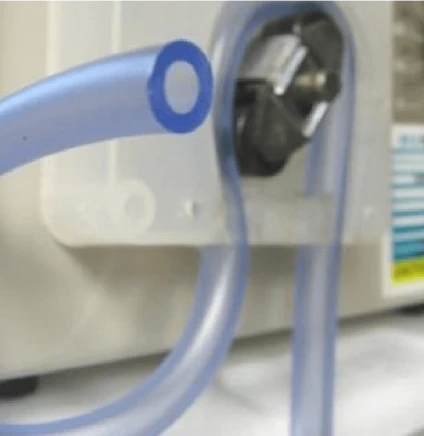
Grayline MD55–PVC High Molecular Weight Polyvinyl Chloride Tubing
Grayline MD55-PVC is a clear flexible tubing made from a high molecular weight, non-phthalate, high purity grade vinyl compound that is suitable for use in short term peristaltic pump applications. This material has a soft, rubber-like feel and can withstand EtO (Ethylene Oxide) and autoclave sterilization methods.
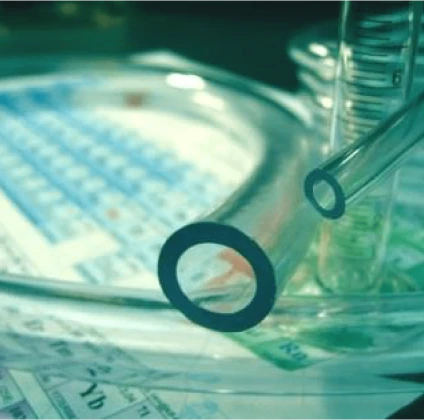
Grayline CX65–PVC Polyvinyl Chloride Tubing
Grayline CX65-PVC is a non-toxic laboratory grade flexible PVC tubing designed for excellent resistance to many fluids, especially inorganic chemicals such as bleach, diluted sulfuric or nitric acid. This tubing performs best in short term, continuous pumping applications where tubing cost is a major concern.
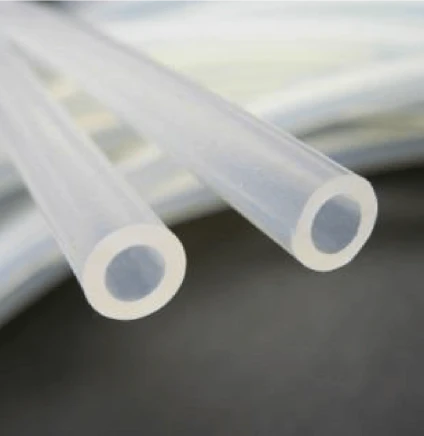
Grayline MD60–PR-SIL Silicone Tubing
Grayline MD60-PR-SIL is a flexible, peroxide-cured medical grade tubing that offers excellent resistance to extreme temperatures. The tubing is soft, pliable, and contains no plasticizers which could leach out, causing flow contamination. It is odorless, tasteless, inert and is ideal for use in both continuous and intermittent peristaltic pump applications.
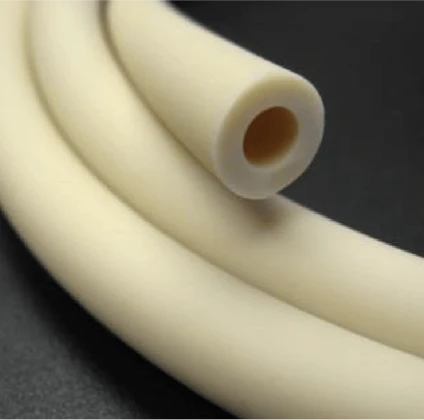
Grayline Everprene-60 Thermoplastic Rubber Tubing
Grayline EVERPRENE-60 tubing is made from a flexible thermoplastic rubber material that is suitable for use in water, food, and beverage applications. It is an good choice for long term peristaltic pump applications because it offers excellent flex fatigue and good tear resistance.
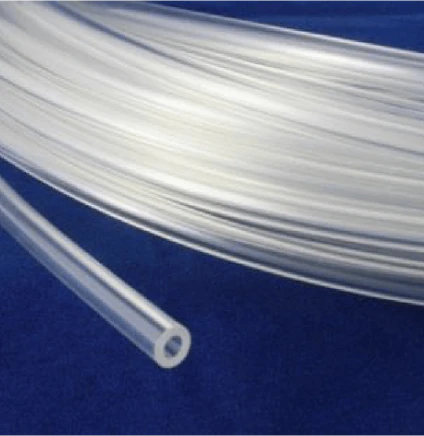
Grayline MD65-TPE Thermoplastic Elastomer Tubing
Grayline MD65-TPE is a clear flexible tubing made from a high purity grade TPE compound. Unlike most TPE materials, MD65-TPE offers a high level of clarity, kink resistance, clamp resilience, and performance characteristics that are similar to PVC. It does not contain DEHP or phthalate plasticizers and is ideal for short-term peristaltic pump application.
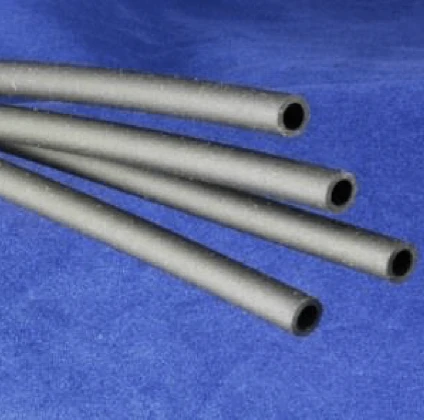
Grayline FL60-VTN Viton Rubber Tubing
Grayline FL60-VTN tubing offers excellent resistance to oils, fuels, lubricants, and most mineral acids. It also resists aliphatic and aromatic hydrocarbons (carbon tetrachloride, benzene, toluene, & xylene). It is ideal for use in peristaltic pump applications that transport highly corrosive acids.
To view this whitepaper in a printable PDF format, please click on the link below: