One of the most common causes of failure for polyethylene components is environmental stress cracking (ESC), a form of low-stress failure that is accelerated by environmental interaction. Surface active chemicals such as those commonly found in detergents are considered an environmental effect that may accelerate failure, while environmental stress cracking resistance (ESCR) is a plastic material’s resistance against it. The following is a discussion of the theory behind this phenomenon as well as experimental results obtained from testing four different types of ethylene-based plastics. It was found that hexene-branched linear-low density polyethylene (h- LLDPE) and crosslinked polyethylene (XLPE) far outperformed butene-branched linear-low density polyethylene (b-LLDPE) and low-density polyethylene (LDPE).
INTRODUCTION
The expansion of the plastic industry in recent decades has made possible the utilization of plastic parts in new and demanding applications in which long life-time service is an essential component. For instance, plastics are being used extensively in fluid flow applications, such as piping for gas distribution and tubing for water transfer [1]. Replacing metals with plastics has made it necessary to use plastics that are mechanically robust and can withstand demanding conditions. Materials that exhibit such required properties as high impact strength, high stiffness, or high tensile strength, however, often suffer from one of the most common forms of failure – low-stress crack rupture. The addition of a surface-active chemical, an environmental effect, accelerates this type of failure, thus this mechanism is termed environmental stress cracking (ESC). A material’s resistance against this type of failure is called environmental stress cracking resistance (ESCR). The ESCR of polyethylene, one of the most widely used plastic materials, is of particular concern in the plastics industry and is the subject of this investigation.
Polymer Structure
Plastics are comprised of a multitude of long “macromolecules” called polymers. These polymer molecules are comprised of long chains of repeating subunits. Interesting to note, the term polymer can be broken down into its Greek roots as follows: ‘poly-’ or ‘many’ and ‘-mer’ or ‘part’ – many parts [2].
In general, plastics can be divided into two categories: semi-crystalline and amorphous. Amorphous plastics are polymers that remain in a disordered state once cooled, whereas semi-crystalline plastics have the ability to form an arrangement of ordered molecules, or crystals [2].
The term semi-crystalline is used, because it is not possible for polymers to be completely crystalline. On a microscopic scale, one can imagine plastic as a bowl of cooked spaghetti; much like the noodles in the bowl, polymer chains intermingle with one another and become entangled [3]. Moreover, in addition to the main polymer chain, side chains can also be found emanating out from the main chain. These side chains, called branching, are similar to the branches of a tree and, depending on the type of side chain and degree of branching, a certain polymer may be able to conform itself into an organized, crystalline state. If a polymer has a bulky side chain (large branch), this makes it difficult to organize into crystals since it reduces their ability to fold itself together. For instance, consider a piece of string and how it can be folded so that it overlaps on itself. Now consider a ball attached to that piece of string; this makes it much more difficult to fold the string back and forth. This is the basis by which semicrystalline and amorphous plastics are comprised.
By understanding the basic structure of polyethylene, it is easy to see how this can affect environmental stress cracking. Throughout a semi-crystalline polymer, there may be small packets of crystals contained within the amorphous matrix, with some polymer chains being so long that they can be in two different crystals at the same time. These molecules, since they tie two crystals together, are called “tie molecules” and play an important role in defining a material’s ESCR. A schematic of this concept is provided in Figure 1.
In general, plastics can be divided into two categories: semi-crystalline and amorphous. Amorphous plastics are polymers that remain in a disordered state once cooled, whereas semi-crystalline plastics have the ability to form an arrangement of ordered molecules, or crystals [2].
The term semi-crystalline is used, because it is not possible for polymers to be completely crystalline. On a microscopic scale, one can imagine plastic as a bowl of cooked spaghetti; much like the noodles in the bowl, polymer chains intermingle with one another and become entangled [3]. Moreover, in addition to the main polymer chain, side chains can also be found emanating out from the main chain. These side chains, called branching, are similar to the branches of a tree and, depending on the type of side chain and degree of branching, a certain polymer may be able to conform itself into an organized, crystalline state. If a polymer has a bulky side chain (large branch), this makes it difficult to organize into crystals since it reduces their ability to fold itself together. For instance, consider a piece of string and how it can be folded so that it overlaps on itself. Now consider a ball attached to that piece of string; this makes it much more difficult to fold the string back and forth. This is the basis by which semicrystalline and amorphous plastics are comprised.
By understanding the basic structure of polyethylene, it is easy to see how this can affect environmental stress cracking. Throughout a semi-crystalline polymer, there may be small packets of crystals contained within the amorphous matrix, with some polymer chains being so long that they can be in two different crystals at the same time. These molecules, since they tie two crystals together, are called “tie molecules” and play an important role in defining a material’s ESCR. A schematic of this concept is provided in Figure 1.
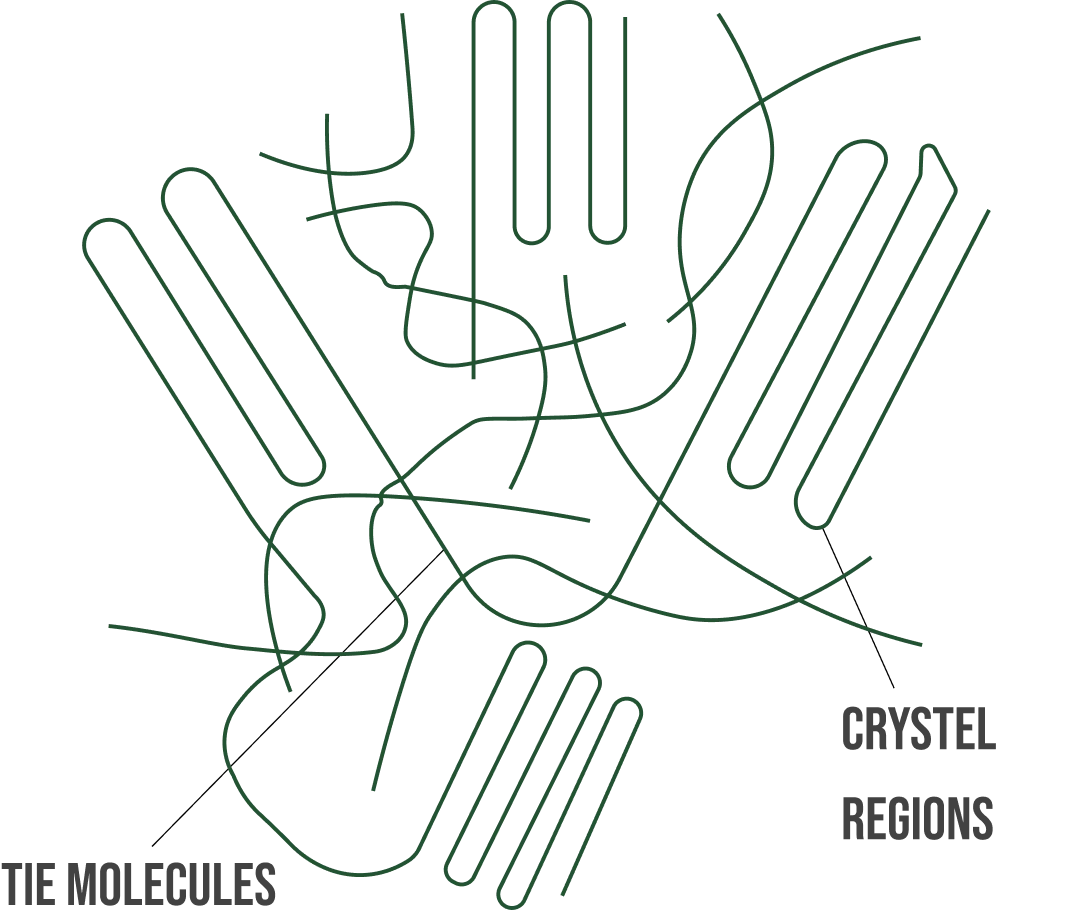
Figure 1: Crystalline and amorphous regions in polyethylene. Tie molecules are polymer chains that start in one crystal and end in another, tying together two crystalline regions [4].
When a plastic part is under mechanical stress it can result in crack formation and propagation, eventually leading to part failure. While this can occur under high stress conditions, one of the most common forms of failure for plastic components is low-stress failure. On the microscopic scale, what occurs through this mechanism is the breaking apart of polymer chains – chains snap apart. This leads to voids within the structure, causing the development of cracks that can propagate and result in part failure. The addition of a surface-active chemical commonly found in soaps or detergents can accelerate this failure mechanism. It has been observed in previous studies, that when environmental stress cracking occurs, polymercrystallinity increases [5].
Furthermore, the location at which polymer chains are most likely to snap apart is the interphase region connecting crystals and the surrounding amorphous region. The reason for this is twofold: a chain cannot break in a crystal because that would not lead to increased crystallinity and a chain is not likely to break far away from a crystal because that would require a high amount of energy to pull the chain into an existing crystal [4]. Therefore, tie molecules provide a strong linkage between crystalline regions in order to strengthen the highly stressed interphase region, meaning a polymer that contains many tie molecules will have better ESCR. There are three different aspects of polymer structure that have a significant impact on ESCR: molecular weight, crystallinity and density, and chain branching.
Furthermore, the location at which polymer chains are most likely to snap apart is the interphase region connecting crystals and the surrounding amorphous region. The reason for this is twofold: a chain cannot break in a crystal because that would not lead to increased crystallinity and a chain is not likely to break far away from a crystal because that would require a high amount of energy to pull the chain into an existing crystal [4]. Therefore, tie molecules provide a strong linkage between crystalline regions in order to strengthen the highly stressed interphase region, meaning a polymer that contains many tie molecules will have better ESCR. There are three different aspects of polymer structure that have a significant impact on ESCR: molecular weight, crystallinity and density, and chain branching.
Molecular Weight
A plastic material is made up of polymer chains varying in length. Each molecule has a certain weight which depends on the length of the chain – longer chains have more weight and shorter chains have less weight. Thus, the weight of a particular plastic is described as the average weight of all of its molecules, also known as molecular weight. The higher the molecular weight, the greater the amount of longer chains. Intuitively, it can be understood that the higher the average chain length, the higher the proportion of tie molecules. These tie molecules act as anchors, holding together two crystals, mitigating the level of stress found in the interphase region. If all other characteristics remain the same, a plastic with a high molecular weight will have better ESCR.
Crystallinity and Density
In addition to molecular weight, crystallinity and density are important ways to describe polymer structure and its influence on ESCR. These two concepts are closely tied together, a polyethylene plastic with high density also has high crystallinity and vice versa. For instance, low density polyethylene (LDPE) can only crystallize up to 40 to 50%. High density polyethylene (HDPE), on the other hand, can crystallize up to 80% [2]. However, crystallinity can have a detrimental effect on the ESCR of polyethylene. A semi-crystalline polymer, such as polyethylene, contains many different crystal regions, not just a few large ones. HDPE will have more of these regions, whereas LDPE will have less. Since the point at which stress is highest among polymer chains resides in the interphase region between crystals and the surrounding amorphous region, a polymer that has many crystals will be more susceptible to ESC failure.
Chain Branching
Similarly tied to ESCR through crystallinity, chain branching also plays an important role in this failure mechanism. Chain branching, as discussed earlier, is the divergence of smaller chains off of the polymer backbone, like the branches of a tree. A polymer that has a high amount of short chain branching will have a lower degree of crystallinity because these side chains hinder the polymer’s ability to fold and become organized. Therefore, due to the lower crystalline level, a high degree of short chain branching will result in better ESCR performance. To illustrate this point, Figure 2 shows the difference in branching between low-density polyethylene (LDPE) and linear low-density polyethylene (LLDPE). LDPE contains long side chains and even has long side chains that branch off of them. LLDPE, on the other hand, contains a controlled degree of branching with short side chains of a consistent length. If a LDPE and LLDPE have the same molecular weight, then the LLDPE material will have better ESCR due to longer primary chains.
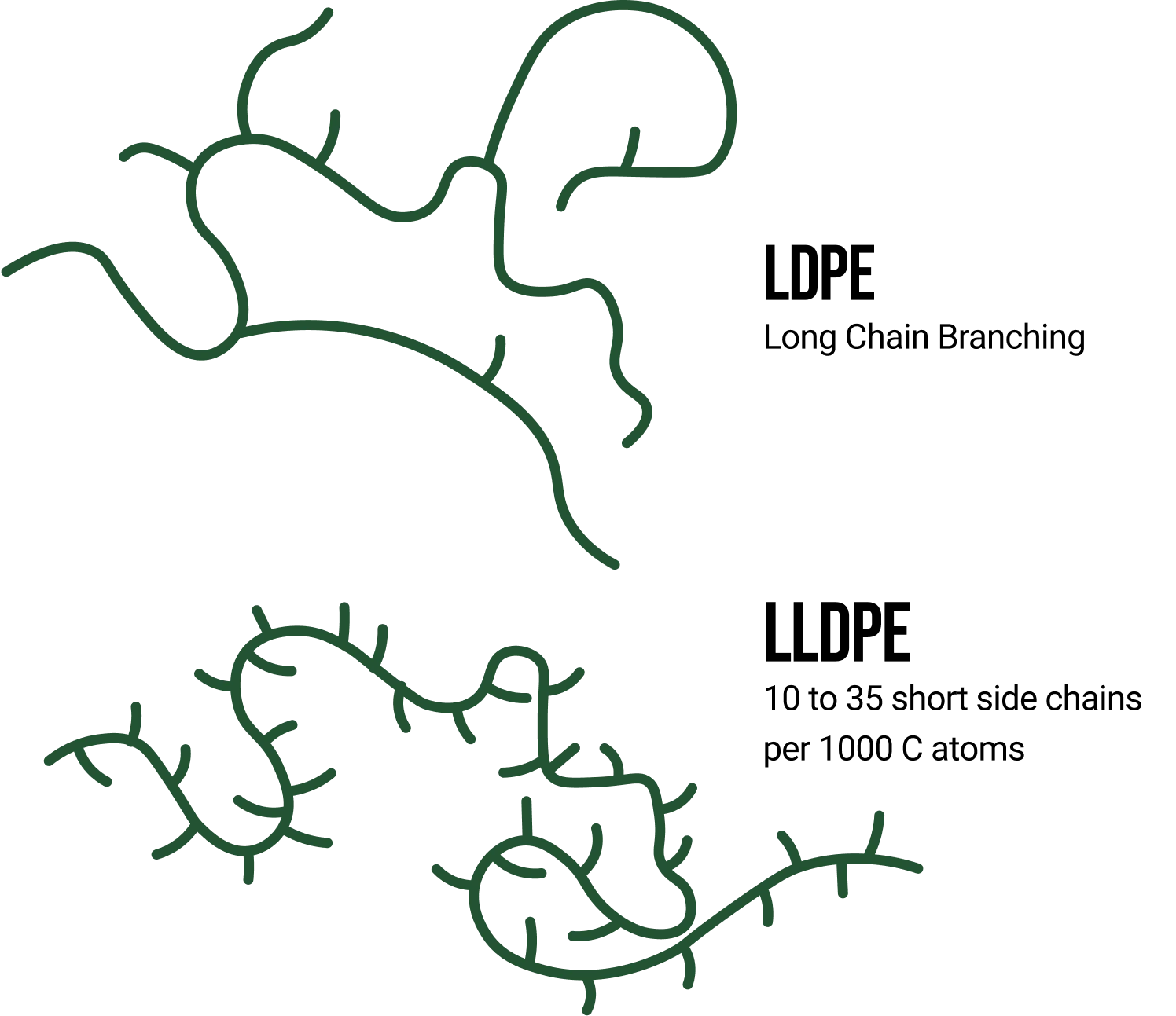
Figure 2: Branching in LDPE and LLDPE [2].
Experiment and Results
ESCR experimentation was conducted at Grayline LLC in order to see how ESCR performance varied among four polyethylene-based plastics: low-density polyethylene (LDPE), butenebranched linear low-density polyethylene (b-LLDPE), hexene-branched linear low-density polyethylene (h-LLDPE), and cross-linked polyethylene (XLPE). All materials were extruded at Grayline under similar processing conditions, with the exception of XLPE which required a postprocessing, chemical cross-linking step. Hexene is a six carbon long side chain, while butene is a three carbon long side chain.
The ESCR testing procedure required a modification to ASTM D1693, an existing test standard to determine ESCR of ethylene plastics. The standard calls for a bent-strip test of ten samples to be immersed in a solution of 10% surfactant at elevated temperatures. Since Grayline is a tubing manufacturer it was not possible to use strips of material, so a specially designed sample holder was made in order to hold bent tubes instead. Furthermore, each sample had a crack initiated prior to being placed in the jar in order to promote failure. The material was determined to have failed when at least five of the samples ruptured.
To help explain the results of the ESCR test, weight crystallinity (Xc), and molecular weight (Mn) were found using differential scanning calorimetry (DSC) and gel permeation chromatography (GPC), respectively. Data for Mn was provided by Westlake Chemical. Since XLPE is cross-linked, it was assumed the material had an infinite molecular weight value (although this is not the case, since the DSC scan resulted in a melt and crystallization peak).
Figure 3 provides the results after (a) 63.5 hours and (b) 135.5 hours, the times after which LDPE and b-LLDPE failed, respectively. Moreover, Table 1 provides the results from ESCR testing as well as Xc and Mn for the respective materials. Both h-LLDPE and XLPE did not fail during the test period of 1000hrs., proving that they had the best resistance to ESC in comparison with LDPE and b-LLDPE.
The ESCR testing procedure required a modification to ASTM D1693, an existing test standard to determine ESCR of ethylene plastics. The standard calls for a bent-strip test of ten samples to be immersed in a solution of 10% surfactant at elevated temperatures. Since Grayline is a tubing manufacturer it was not possible to use strips of material, so a specially designed sample holder was made in order to hold bent tubes instead. Furthermore, each sample had a crack initiated prior to being placed in the jar in order to promote failure. The material was determined to have failed when at least five of the samples ruptured.
To help explain the results of the ESCR test, weight crystallinity (Xc), and molecular weight (Mn) were found using differential scanning calorimetry (DSC) and gel permeation chromatography (GPC), respectively. Data for Mn was provided by Westlake Chemical. Since XLPE is cross-linked, it was assumed the material had an infinite molecular weight value (although this is not the case, since the DSC scan resulted in a melt and crystallization peak).
Figure 3 provides the results after (a) 63.5 hours and (b) 135.5 hours, the times after which LDPE and b-LLDPE failed, respectively. Moreover, Table 1 provides the results from ESCR testing as well as Xc and Mn for the respective materials. Both h-LLDPE and XLPE did not fail during the test period of 1000hrs., proving that they had the best resistance to ESC in comparison with LDPE and b-LLDPE.
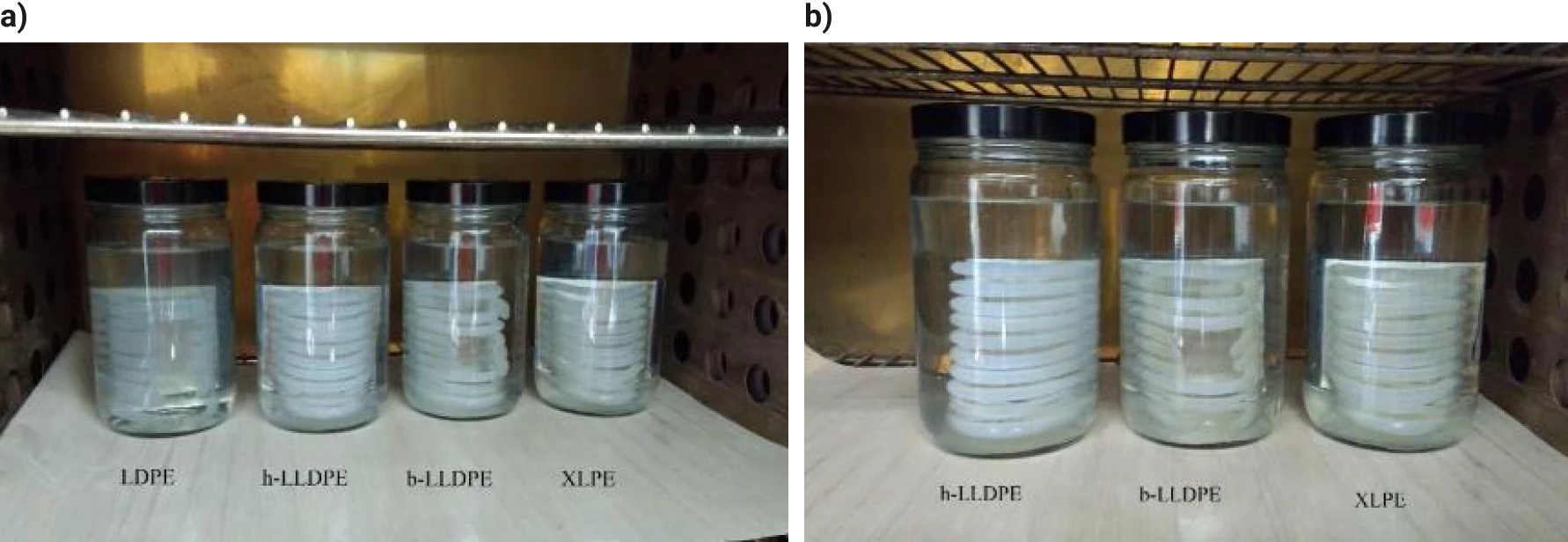
Figure 3: Test results for ESCR test: (a) after 63.5hrs LDPE failed; (b) after 135.5hrs b-LLDPE failed.
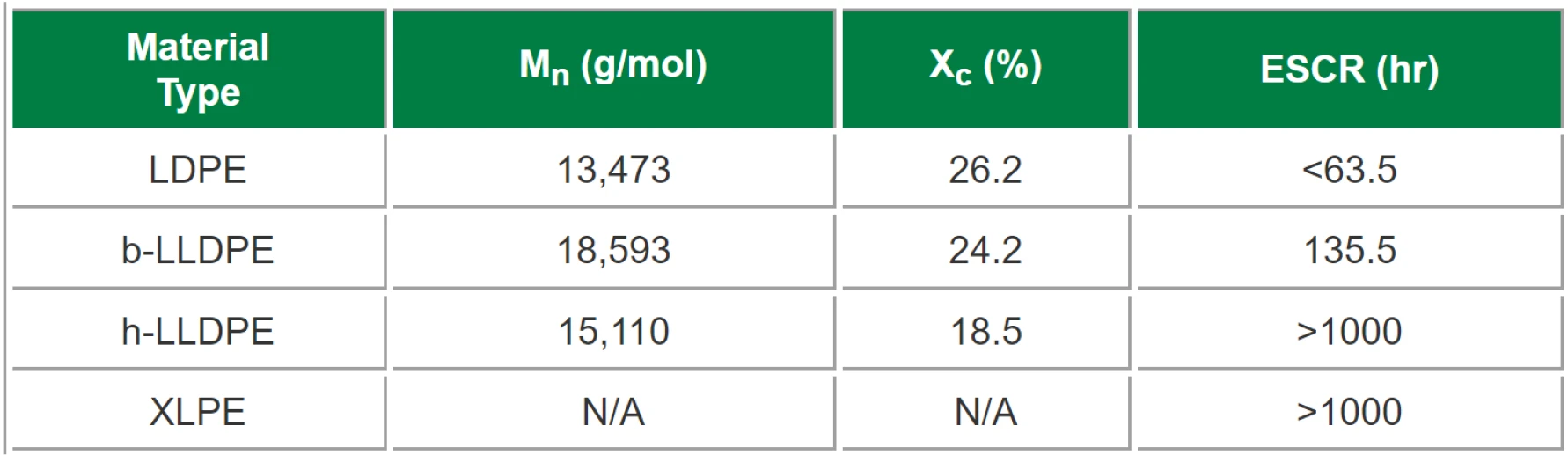
Table 1: Molecular Characterization of Polyethylene [6]
In addition to these results, Figure 4 shows the relationship between ESCR with (a) Xc and (b) Mn. There is a strong correlation between ESCR and degree of crystallinity, showing a decrease in failure time with respect to increasing crystallization, which follows the expected trend. There is not, however, any noticeable correlation with molecular weight. It was suggested earlier that ESCR increases as molecular weight increases, since longer chains have a greater potential to act as tie molecules. However, ESCR will not always increase with increasing molecular weight, because branching also plays a significant role in determining a material’s Mn. For instance, looking at the difference in performance between b-LLDPE and h-LLDPE, one would assume that b-LLDPE would have high ESCR since it has higher Mn. This is not the case, as it exhibits far worse performance. The difference in crystallinity most likely has more of an impact on performance, especially since these two materials have relatively similar Mn values. b-LLDPE contains a higher degree of crystallization, meaning it has more interphase locations which are vulnerable to stress cracking. Butene, a three carbon-long chain, and hexene, a six carbon-long chain, are the side chains for b-LLDPE and h-LLDPE, respectively. Since hexene is a longer and more bulky side chain, it can disrupt crystal formation more readily, which helps to explain why h-LLDPE exhibited a lower degree of crystallinity.
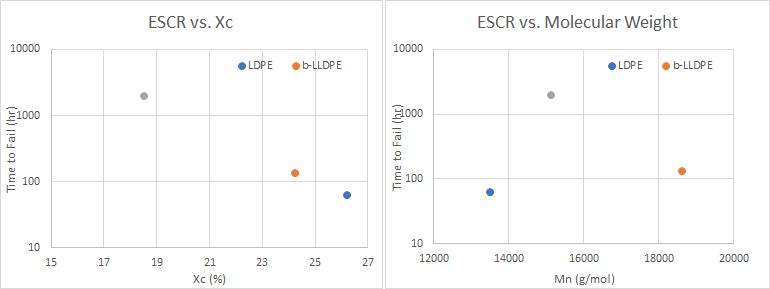
Figure 4: (a) ESCR as a function of crystallinity. The point on the graph indicating h-LLDPE was chosen to be 2000hrs in order to show that this material had a failure time greater than 1000hrs; (b) ESCR as a function of molecular weight.
Experiment and Results
This study was conducted in order to determine which polyethylene-based material would provide the longest resistance to environmental stress cracking. By using a modified version of ASTM D1693, it was found that h-LLDPE and XLPE far outperformed b-LLDPE and LDPE, resulting in a failure time of >1,000 hours.
A good correlation between ESCR performance and crystallinity was found, showing that an increase in the amount of crystallinity and the corresponding interphase regions can have a detrimental impact on product lifetime. The influence of molecular weight on ESCR performance did not show significant correlation. This is most likely because crystallinity had a greater impact on performance and since the difference in molecular weight between LDPE, b-LLDPE, and h- LLDPE may not have been significant enough to provide adiscernable impact.
A good correlation between ESCR performance and crystallinity was found, showing that an increase in the amount of crystallinity and the corresponding interphase regions can have a detrimental impact on product lifetime. The influence of molecular weight on ESCR performance did not show significant correlation. This is most likely because crystallinity had a greater impact on performance and since the difference in molecular weight between LDPE, b-LLDPE, and h- LLDPE may not have been significant enough to provide adiscernable impact.
References
[1] Cazenave, J., Sixou, B., and Seguela, R. “Structural Approaches of Polyethylene Environmental Stress-Crack Resistance.” Oil and Gas Science and Technology. Vol. 61, No. 6, pp. 735-742 (2006).
[2] Osswald, Tim A., Menges, Georg. Materials Science of Polymers for Engineers. Munich: HanserPublishers, 2010.
[3] “Introduction to Polymers.” Cmu.edu, Carnegie Mellon University.
[4] Al-Zubi, Raed, Strong, A. Brent, and Lampson, Marshall. “Understanding Environmental Stress Crack Resistance (ESCR) in Rotomolded Polyethylene Tanks.” Poly Processing Company: Team Innovation.
[5] Hamid, S. Handbook of Polymer Degradation. 2nd edition. New York: Marcel Dekker Inc, 2000.
[6] Westlake Chemical. “MWD Comparison – EC1550 LF1050 LF2051.” Dataset.
[2] Osswald, Tim A., Menges, Georg. Materials Science of Polymers for Engineers. Munich: HanserPublishers, 2010.
[3] “Introduction to Polymers.” Cmu.edu, Carnegie Mellon University.
[4] Al-Zubi, Raed, Strong, A. Brent, and Lampson, Marshall. “Understanding Environmental Stress Crack Resistance (ESCR) in Rotomolded Polyethylene Tanks.” Poly Processing Company: Team Innovation.
[5] Hamid, S. Handbook of Polymer Degradation. 2nd edition. New York: Marcel Dekker Inc, 2000.
[6] Westlake Chemical. “MWD Comparison – EC1550 LF1050 LF2051.” Dataset.
To view this whitepaper in a printable PDF format, please click on the link below: