Introduction to Heat Shrink Tubing
The following information will help you determine what type of heat shrink product is most appropriate for your application. It will serve as a step-by-step guide to assure you that you’re buying the correct product, and it will help you to identify the most cost-effective solution while ensuring that what you buy is going to meet your needs. In this section, the basics of heat shrink tubing are discussed.
Introduction to Heat Shrink Tubing
Heat shrink tubing is manufactured using a two-step process. The first step involves standard extrusion procedures, after which a secondary process makes the tubing heat-shrinkable. Although the details of this secondary process are proprietary, heat and force are used to expand the diameter of the tubing. The tubing is then cooled to room temperature while in the expanded state. If the tubing is later exposed to a sufficient amount of heat, it will shrink down to its original size as long as it is not restrained from doing so.
Introduction to Heat Shrink Tubing
There are a number of useful applications for heat shrink tubing. Below is a list of its various uses:
- to provide electrical insulation (covering terminals, splices, wire repairs, or other connectors)
- to bundle loose items (most commonly wires in wire harnesses)
- as a protective covering, safeguarding from:
- abrasion
- cutting
- chipping
- peeling
- scuffing
- denting
- low impact
- to provide an environmental seal, protecting sensitive components from contaminants such as moisture and chemicals which might cause oxidation and/or corrosion of the components
- to provide strain relief
- to provide thermal insulation
- to color-code specific items
- to change the surface finish of an object
- to identify a component (with printing, a custom color, etc)
Step 1: Understand Your Application
The most important aspect of choosing the appropriate heat shrink product for your needs is to understand and define all that is necessary for your application. The only way to ensure that you’re getting the most appropriate, cost-effective product is to fully understand your application and the requirements that need to be met.
Sizing Requirements
Regardless of whether you’re using heat shrink tubing in an electrical application, as a strain relief, as a protective covering, or for any other reason, determining the correct size is of the utmost importance. The two most important dimensions to measure for your application are the largest diameter that the expanded sleeve needs to slide over and the smallest diameter that the tubing needs to completely cover after shrinking. These two dimensions will be used later in Step 2 to help you determine the required size and shrink ratio for your tubing. If either of these locations has a non-circular profile, you will need to convert the non-circular perimeter to a diameter. To do this you must measure the total perimeter at this location and divide that number by pi (or 3.14). This will give you an “effective” diameter which you can use to help determine the tubing size you need. For the component on the right side of the figure on the following page, the largest diameter is equal to (A+A+B+B)/pi and the smallest diameter is simply d.
Another important dimension to consider is minimum wall thickness. A certain minimum wall thickness might be required due to the electrical requirements of your application. Or, if the tubing is going to be subjected to excessive abrasion or wear, you may wish to have a heavier wall thickness than the standard size offers. In addition to defining your required minimum wall thickness, it is also necessary to determine the diameter at which this wall thickness will be required. This information is critical in choosing the required tubing size in Step 2.
Another important dimension to consider is minimum wall thickness. A certain minimum wall thickness might be required due to the electrical requirements of your application. Or, if the tubing is going to be subjected to excessive abrasion or wear, you may wish to have a heavier wall thickness than the standard size offers. In addition to defining your required minimum wall thickness, it is also necessary to determine the diameter at which this wall thickness will be required. This information is critical in choosing the required tubing size in Step 2.
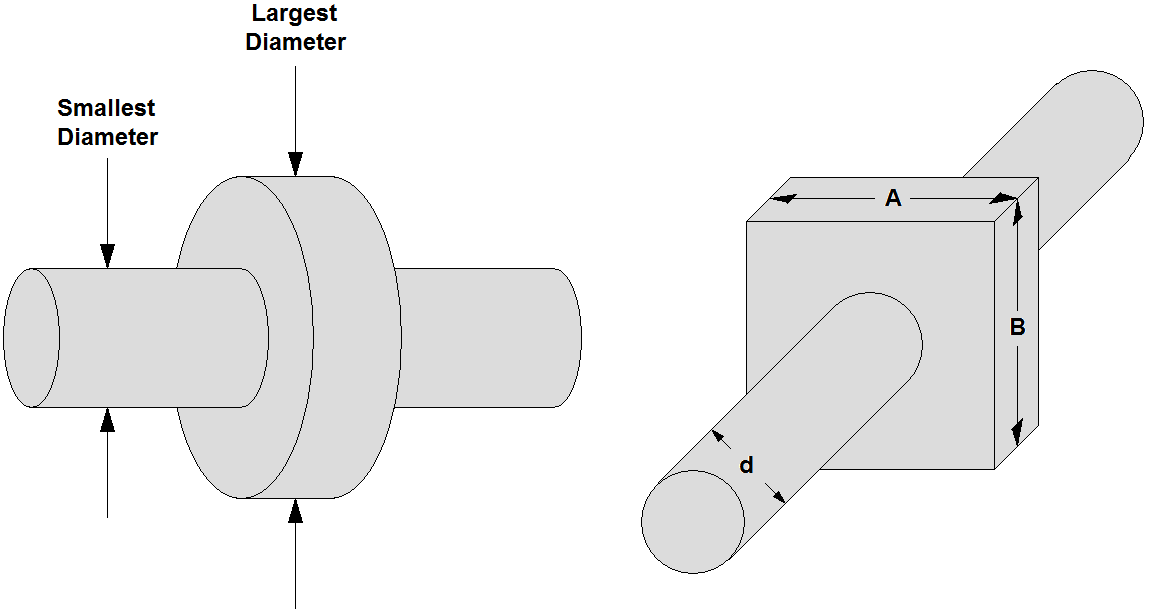
Electrical Property Requirements
If your heat shrink tubing is going to provide electrical insulation or bundle electrical wires, it is likely that it needs to meet certain regulatory guidelines. In order to choose the correct product for your application, you’ll need to know if any UL/CSA (Underwriters Laboratories / Canadian Standards Association), ASTM (American Society for Testing and Materials), AMS (Aerospace Material Specification), EU (European Union), or other automotive or military specifications need to be met. These guidelines usually cover common electrical requirements such as dielectric strength and flame resistance. Other possible electrical requirements could be that the tubing must be free of halogens or that it must be made out of a specific material. Make sure you understand all of the electrical requirements before you choose your heat shrink product.
Operating Environment
Another critical step in defining the requirements of your heat shrink tubing application is to understand the environment in which the tubing will operate. For example, will the tubing be subjected to excessive abrasion or flexing? Will the tubing come into contact with any oils, greases, fuels, chemicals, or other fluids? It is also important to know if the tubing will be used indoors or outdoors. If it is going to be used outdoors it could be subjected to excessive UV exposure. If it is going to be lying on or buried below the ground, it may need to have superior resistance to fungus growth. Finally, an enhanced environmental seal (as obtained with adhesive-lined heat shrink tubing) may be needed to protect any sensitive portion of the object the tubing is covering. All of these factors need to be considered prior to selecting your heat shrink product.
Step 2: Determine the Required Tubing Size
The next step is to determine the most appropriate tubing size for your application. Using the measurements you obtained in Step 1, you’ll need to define the following tubing dimensions that best suit your needs: minimum expanded ID, maximum recovered ID, and minimum recovered wall thickness. This section will explain each of these tubing dimensions and how they relate to your application measurements found in Step 1.
Expanded and Recovered Inside Diameters
Heat shrink tubing is traditionally specified by the minimum original (“expanded”) inside diameter and the nominal shrink ratio. However, a good heat shrink product datasheet will not only list the minimum expanded ID and nominal shrink ratio of the tubing, but also its maximum recovered ID. First, check that the minimum expanded ID of the tubing is greater than the largest diameter that the sleeve needs to slide over (using the measurement you made in Step 1). Then, check that the maximum recovered ID of the tubing is less than the smallest diameter that needs to be completely covered (also measured in Step 1). Please see the figure below which illustrates these tubing dimensions:
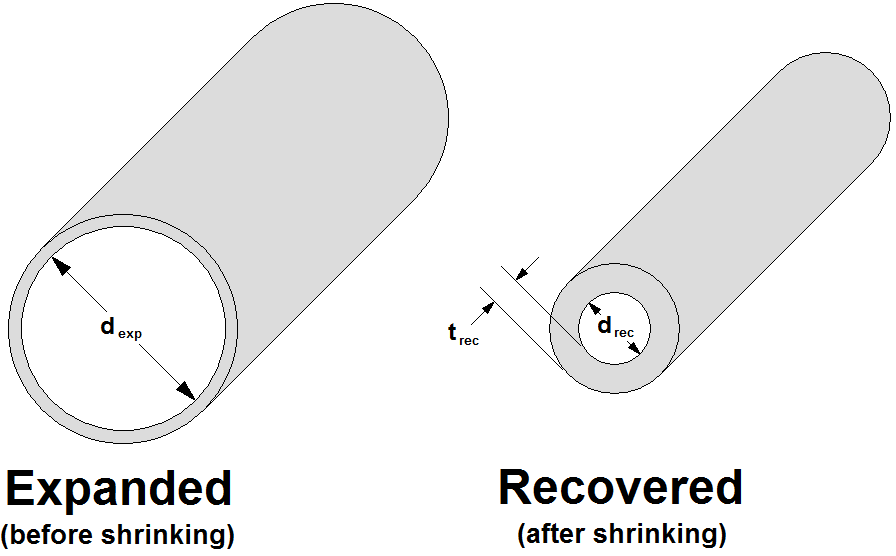
Shrink Ratio
If the product datasheet does not have maximum recovered ID listed, you can estimate it using the minimum expanded ID and the shrink ratio. If a heat shrink product has a 3:1 shrink ratio and the minimum expanded ID is 0.750”, then the maximum recovered ID should be 0.750”/3 or 0.250”.
Wall Thickness
Now that you have determined the required minimum expanded ID and maximum recovered ID (or shrink ratio), you will need to determine the minimum recovered wall thickness needed for your application. The wall thickness of a heat shrink product is traditionally specified as the minimum thickness at the fully recovered stage (see right side of the figure above). Therefore, in order to determine the required wall thickness of your heat shrink product you must use another measurement from Step 1: your required minimum wall thickness and the diameter at which that wall thickness is required. If the diameter of what you are covering is greater than the maximum fully recovered diameter of the tubing, the final wall thickness will be less than what is specified on the datasheet. This is illustrated in the figure below:
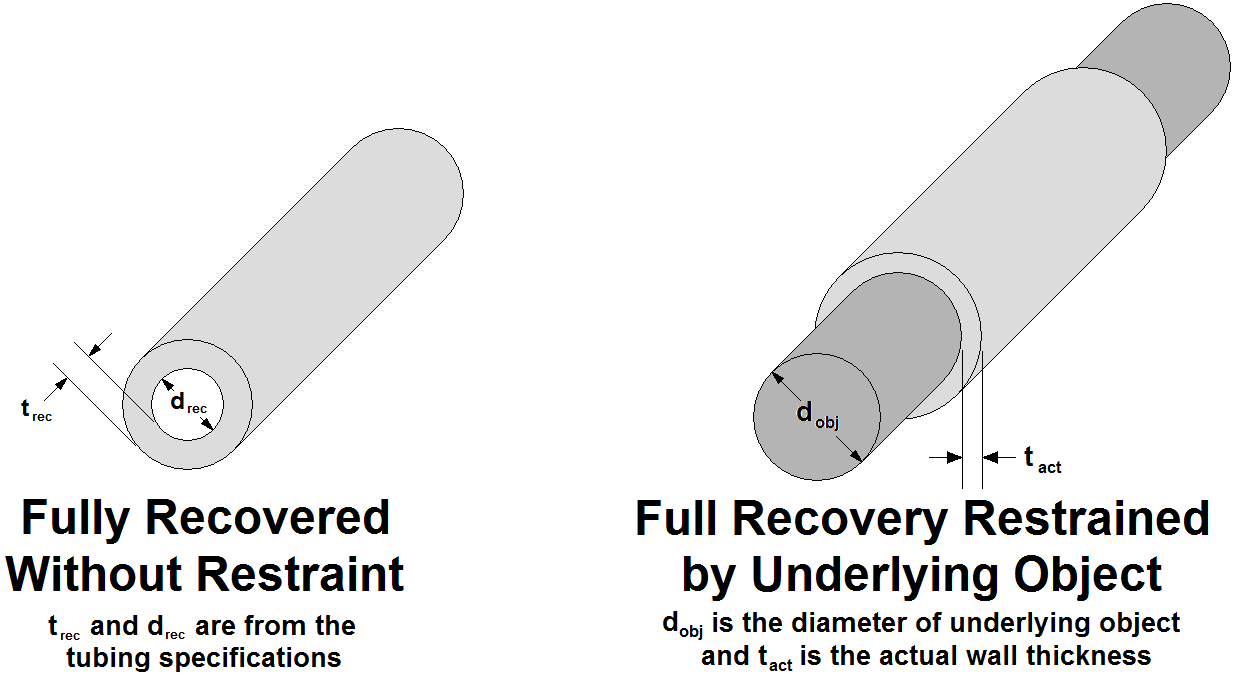
The dimension trec is the wall thickness that would result if your heat shrink tubing were allowed to shrink fully without restraint. However, since your object is restraining the tubing from shrinking fully, you’ll need to determine the required tact before you can specify trec for the tubing. The approximate relationship between the two thickness dimensions is as follows:
drec * trec + trec2 = dobj * tact + tact2
A much simpler relationship can be used to solve for trec or tact. This is a further approximation, but acceptable for this purpose*
:trec = (dobj * tact)/ drec or tact = (drec * trec)/ dobj
* This relationship can be off by 10-20% with heavier wall thicknesses. Contact your tubing supplier to ensure that you’re getting the correct actual wall thickness with a given heavy-walled tubing size.
Variable Key
tact = actual wall thickness after shrinking onto the underlying object
dobj = diameter of the underlying object
trec = specified recovered wall thickness of tubing
drec = specified recovered diameter of tubing
drec * trec + trec2 = dobj * tact + tact2
A much simpler relationship can be used to solve for trec or tact. This is a further approximation, but acceptable for this purpose*
:trec = (dobj * tact)/ drec or tact = (drec * trec)/ dobj
* This relationship can be off by 10-20% with heavier wall thicknesses. Contact your tubing supplier to ensure that you’re getting the correct actual wall thickness with a given heavy-walled tubing size.
Variable Key
tact = actual wall thickness after shrinking onto the underlying object
dobj = diameter of the underlying object
trec = specified recovered wall thickness of tubing
drec = specified recovered diameter of tubing
Length & Longitudinal Shrinkage
If tubing length is a critical dimension for your application, longitudinal shrinkage must be considered. In addition to shrinking in diameter upon the application of heat, heat shrink tubing may also shrink in length. The amount of length reduction depends upon the amount of diameter reduction as well as manufacturing processing variables, but it is generally about 15% of the original length or less. Because longitudinal shrinkage depends on various tubing characteristics, it is best to determine the expected longitudinal shrinkage of your heat shrink product from your supplier.
Step 3: Choose the Appropriate Heat Shrink Material
Once you have defined all that is necessary for your application and have chosen the appropriate tubing size, you are ready to choose your heat shrink material. Often there are multiple products that will meet your needs, so it is important to also know the cost and availability of each option. This section will examine how to choose the right material by differentiating each by cost and capability.
Available Heat Shrink Tubing Materials
A common misconception among heat shrink users is that there is only one heat shrink material. While polyolefin is the most widely used material, PVC heat shrink tubing can be a cost-effective alternative for many applications. In addition to the polyolefin and PVC material families, specialty heat shrink tubing is available in various fluoropolymers and elastomeric materials. Within each of these material families are many different compounds which are designed to excel in certain environments and/or meet particular specifications.
PVC versus Polyolefin
Polyolefin is the most commonly used heat shrink material. Its advantages lie in the cross-linking of polymer chains, which allow it to withstand high temperatures in the 125°C-135°C (257°F -275°F) range. However, a common misconception is that “heat shrink is heat shrink”; that is, all heat shrink is the same and it doesn’t matter what you choose. While PVC cannot withstand the highest temperatures that polyolefin can, there are many advantages to using PVC. The most important benefit to using PVC heat shrink tubing is lower cost. PVC generally costs anywhere from 10% to 60% less than polyolefin. If your application involves an operating environment in which the continuous high temperature is 105°C (221°F) or less, you should strongly consider PVC heat shrink for the cost savings alone. In addition to the significant price difference, PVC also offers brighter, more vibrant colors than polyolefin as well as considerably better clarity in its clear version. Custom colors and transparent tints are also available with PVC heat shrink, but typically not with polyolefin heat shrink. Please see the photos on the following page which compare the colors and clarity of polyolefin and PVC heat shrink:
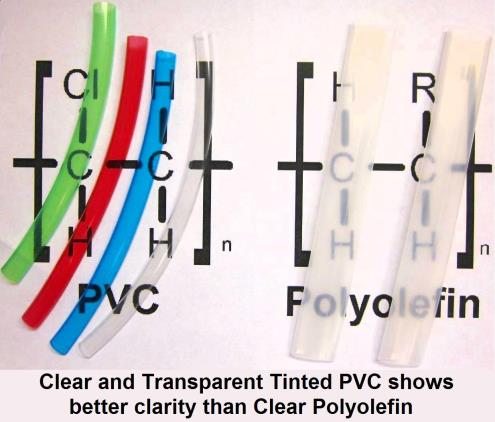
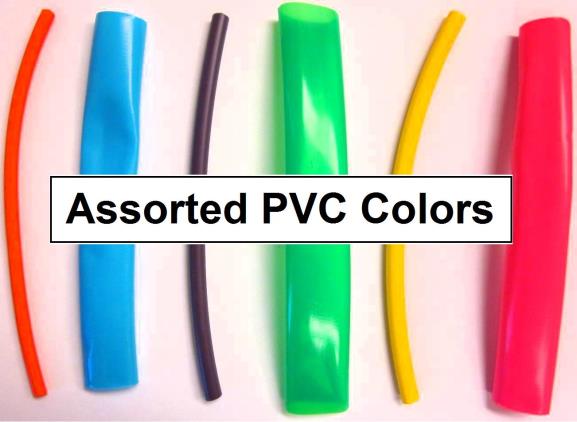
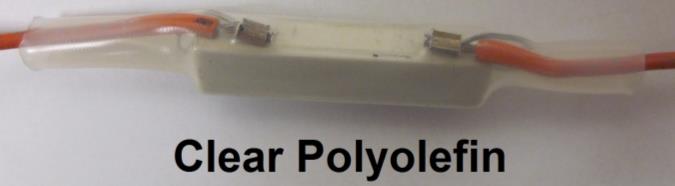
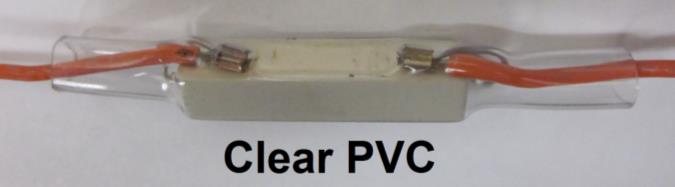
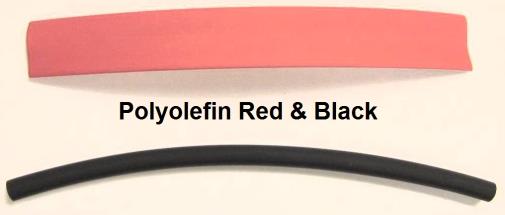
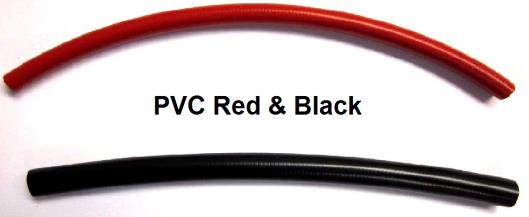
Two other advantages PVC holds over polyolefin are: 1) Clear PVC is flame retardant, while clear polyolefin is not, and 2) PVC is much tougher than polyolefin, with better tensile strength and abrasion resistance. If your operating temperature is 105°C (221°F) or less, it is strongly recommended that you consider PVC as a material option.
Adhesive-Lined Heat Shrink Tubing
Adhesive-lined (or “dual wall”) polyolefin heat shrink tubing is a specialty product that has a wide variety of uses. This product is simply a standard polyolefin tube that has an inner-liner of adhesive that melts and flows at the same temperature at which the polyolefin tubing shrinks. As heat is applied and the tubing is shrinking, the flowing adhesive fills voids and conforms to the underlying shape. This forms an environmental seal, protecting the underlying component(s) from moisture or other contaminants. An example of the use of adhesive-lined tubing is shown in the photo below:
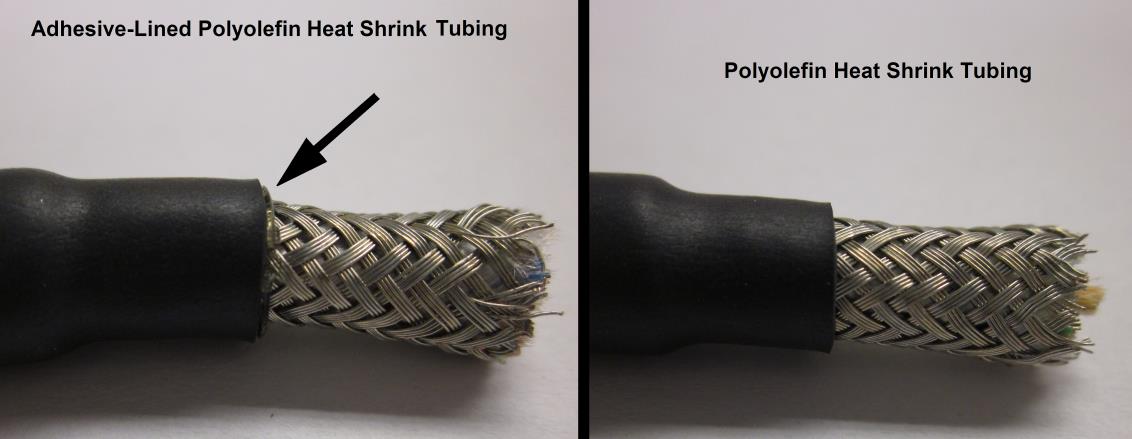
Other Heat Shrink Materials
In addition to the products mentioned above, there are also other specialty heat shrink products available. These products all offer unique qualities such as extreme temperature resistance, exceptional chemical/fluid compatibility, and/or superior mechanical properties. Among these specialty products are fluoropolymers (PTFE/FEP/PFA), chlorinated polyolefin, elastomeric polyolefin, polyvinylidene fluoride (PVDF), and fluoroelastomers. Due to the enhanced qualities of these products, they are significantly more costly than the previously-mentioned products. In some cases, the price differences are extreme. The diagram below gives you a simple, generic comparison of the price differences for a sampling of heat shrink materials:
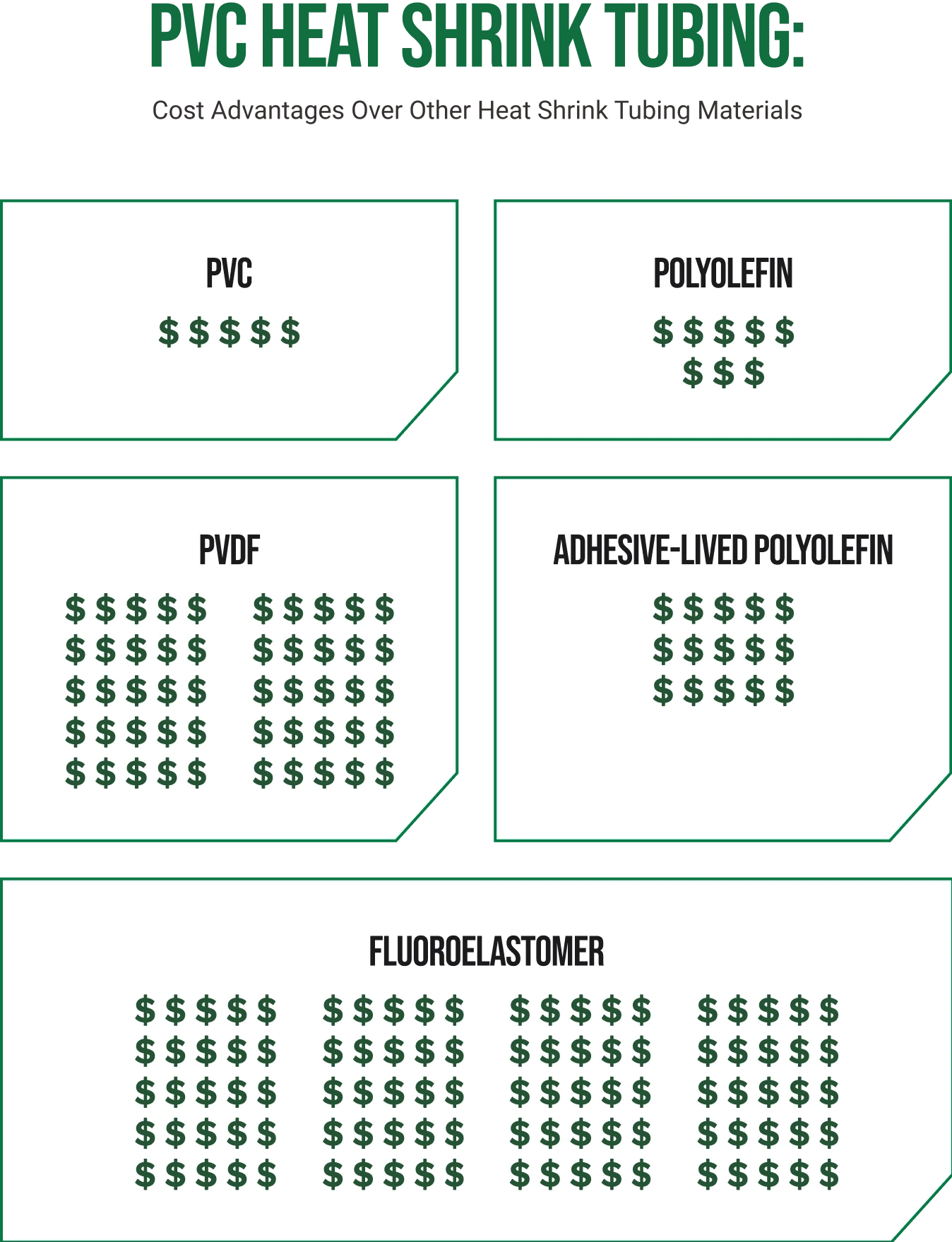
Step 4: How to Use Heat Shrink Tubing
This section will discuss various heating methods commonly used to shrink heat shrink tubing. It will also provide some tips to keep in mind when using and storing the tubing.
Heating Methods
The most common method of shrinking heat shrinkable tubing onto underlying components is through the use of a hand-held heat gun. However, for higher production volumes the preferred method of shrinking the tubing is to use a flow-through oven. This will ensure a complete recovery of the tubing by evenly exposing it to sufficient heat for a satisfactory period of time. For PVC it is recommended that the tubing be exposed to 150°C (300°F) for three minutes. This will allow sufficient time at temperature to achieve a full recovery. At very high temperatures PVC will begin to soften, however, so increasing the temperature beyond 150°C in order to save time could produce negative results. Polyolefin, on the other hand, can withstand shrink temperatures much higher than 150°C. It is still recommended that the tubing be exposed to 150°C for three minutes in a flow-through oven, but in the interest of reducing processing time you can experiment with the use of higher oven temperatures. Lastly, another method occasionally encountered is the use of focused light (as emitted by halogen bulbs) to shrink the tubing.
Storage Conditions
In order to avoid premature recovery, PVC heat shrink tubing must be stored at temperatures below 90°F (32°C) and out of direct sunlight. If these storage guidelines are adhered to, there should be no concerns over shelf life of this product. Polyolefin, on the other hand, has a greater ability to withstand elevated storage temperatures and therefore there should be no shelf life concerns.
Minimizing Longitudinal Shrinkage
If your application calls for a long length of heat shrink tubing, there is a way to minimize and possibly eliminate longitudinal shrinkage. First, apply heat to each end of the tube with a heat gun, which will secure the tubing ends to the underlying component(s). Then complete the shrinking process along the remaining middle section of the tubing using a flow-through oven or heat gun.
Step 5: Availability of Heat Shrink Products through Grayline LLC
This section will highlight the heat shrink products that are available through Grayline Inc., as well as the custom services that can be provided.
Custom PVC Heat Shrink Tubing
Grayline HS105C, a UL-rated heat shrink PVC tubing product, is available in a vast array of custom sizes and colors. Within certain limitations, Grayline can manufacture HS105C in a custom ID and wall thickness to meet the requirements of your application. HS105C comes in many colors, including crystal clear, transparent tints, and a wide range of solid colors, even including glow-in-the-dark. Grayline also offers custom color matching for appearance-critical applications. HS105C is also available in custom shrink ratios.
Chemically Cross-Linked Polyolefin
Grayline is one of the very few manufacturers in the world to offer chemically cross-linked polyolefin heat shrink tubing. Although it does not have the flame-retardant properties of irradiated polyolefin, it can be manufactured in custom sizes and colors. Since this product does not need to be irradiated, small-quantity production runs are cost effective. If your polyolefin heat shrink application calls for a special size and/or a custom color, Grayline GP125 is your only available option.
Other Heat Shrink Materials
In addition to the products mentioned above, Grayline offers various polyolefin, adhesive-lined, fluoropolymer, and fluoroelastomer heat shrink tubing. A full listing of heat shrink products supplied by Grayline can be found at www.graylineinc.com/wire-harness-electrical-tubing/heat-shrinkable-tubing. For wire harness applications, these products are designed to meet the rigorous specifications of UL/CSA, ASTM, AMS, EU, and other various automotive and military specifications.
Additional Services Offered by Grayline
Both PVC and polyolefin heat shrink tubing can be printed on or hot stamped. This printing can be used to indicate part numbers, your company name, logo or contact information, safety warnings, instructions for use, or date of manufacture. Heat shrink tubing from Grayline can be supplied either on reels or cut-to-length.
Conclusion
The preceding information is intended to serve as a basic guideline for new users of heat-shrinkable tubing. If you are interested in any of the products mentioned above or if you have any questions, please do not hesitate to contact Grayline at (800) 669-7986 or You can also visit the Grayline website at www.graylineinc.com.
Below is a partial list of the heat shrinkable tubing products currently offered by Grayline. The links will take you to the product page on Grayline’s website.
Below is a partial list of the heat shrinkable tubing products currently offered by Grayline. The links will take you to the product page on Grayline’s website.
Grayline Heat Shrinkable Tubing Products
HS105C - PVC Heat Shrink Tubing, 2:1 UL/CSA VW-1
GP-125 - Chemically Cross-linked Polyolefin Heat Shrink Tubing, General Purpose, 2:1
SL2535 - Polyolefin Heat Shrink Tubing, 2:1
SL2535CL - Polyolefin Heat Shrink Tubing, 2:1, Clear
SL125 - Polyolefin Heat Shrink Tubing, 2:1, Highly Flame Retardant
SL3X - Polyolefin Heat Shrink Tubing, 3:1
AL2X - Polyolefin Heat Shrink Tubing, Adhesive Lined, 2:1
AL3X - Polyolefin Heat Shrink Tubing, Adhesive Lined, 3:1
AL4X - Polyolefin Heat Shrink Tubing, Adhesive Lined, 4:1
MWT - Polyolefin Heat Shrink Tubing, Medium Wall, Adhesive Lined, 3:1
HWT - Polyolefin Heat Shrink Tubing, Heavy Wall, Adhesive Lined, 3:1
MF392 - Modified Fluoroelastomer Heat Shrink Tubing, 2:1
NHS - Chlorinated Polyolefin Heat Shrink Tubing, 2:1
PVDF - Modified Polyvinylidene Fluoride Heat Shrink Tubing, 2:1
GP-125 - Chemically Cross-linked Polyolefin Heat Shrink Tubing, General Purpose, 2:1
SL2535 - Polyolefin Heat Shrink Tubing, 2:1
SL2535CL - Polyolefin Heat Shrink Tubing, 2:1, Clear
SL125 - Polyolefin Heat Shrink Tubing, 2:1, Highly Flame Retardant
SL3X - Polyolefin Heat Shrink Tubing, 3:1
AL2X - Polyolefin Heat Shrink Tubing, Adhesive Lined, 2:1
AL3X - Polyolefin Heat Shrink Tubing, Adhesive Lined, 3:1
AL4X - Polyolefin Heat Shrink Tubing, Adhesive Lined, 4:1
MWT - Polyolefin Heat Shrink Tubing, Medium Wall, Adhesive Lined, 3:1
HWT - Polyolefin Heat Shrink Tubing, Heavy Wall, Adhesive Lined, 3:1
MF392 - Modified Fluoroelastomer Heat Shrink Tubing, 2:1
NHS - Chlorinated Polyolefin Heat Shrink Tubing, 2:1
PVDF - Modified Polyvinylidene Fluoride Heat Shrink Tubing, 2:1
To view this whitepaper in a printable PDF format, please click on the link below: